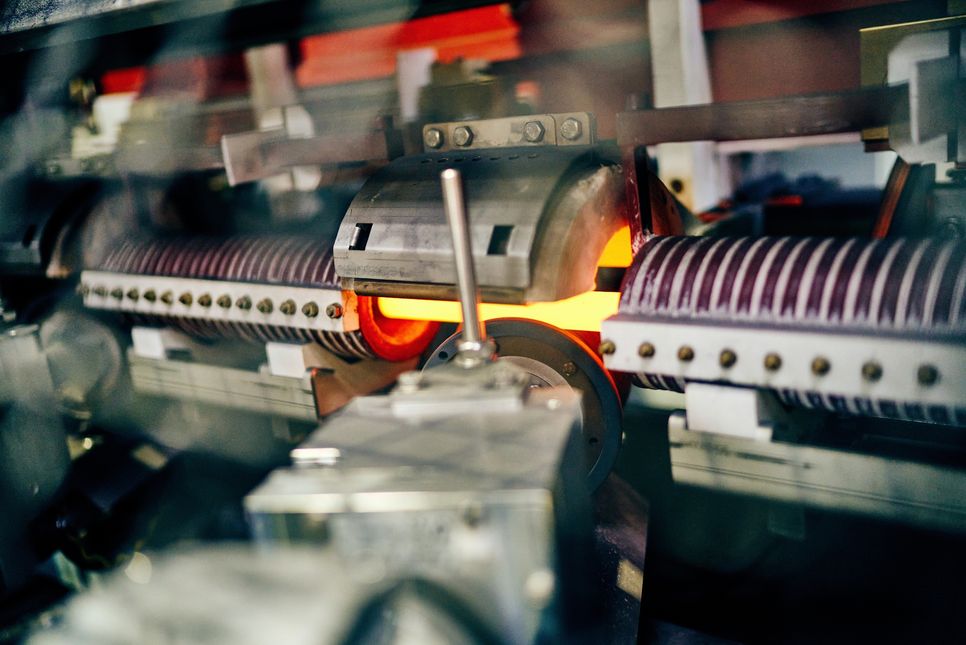
Osnabrück/Georgsmarienhütte, 28 February 2024
GMH secures access to the wind power industry with its first inductive single-bar tempering plant
Georgsmarienhütte launches operations at its first inductive single-bar tempering plant (EVA), and is already planning a second system. Through a double-digit million investment, subsidised by the federal government, GMH Gruppe is opening up new markets and making progress towards achieving climate neutrality.
The Georgsmarienhütte site, GMH Gruppe’s largest production plant, can now meet even higher standards of product strength and toughness in its future steel production, allowing this key material to be used increasingly in the wind power and mechanical engineering industries. This has been made possible with the company’s new, fully automated, inductive single-bar tempering plant (EVA).
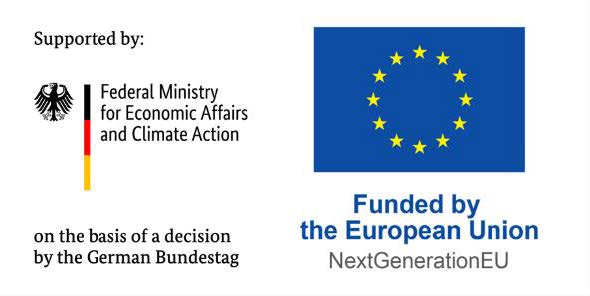
The company is investing around 21.5 million euros in the plant and has separately received a subsidy of 880,000 euros out of the “decarbonisation in industry” funding programme from the Federal Ministry of Economics in Germany and the EU. Unlike GMH’s previous steel tempering process, the EVA is fully automated. This means individual steel bars no longer need to be reworked manually after heating, which is a labour-intensive and risky process. Production efficiency and occupational safety have therefore been enhanced, while the quality of GMH’s steel has been further improved.
Dipl.-Ing. Volker Glane, Head of Technology Heat Treatment and Testing Technology at Georgsmarienhütte GmbH, explains how the EVA works: “The inductive tempering of individual steel bars in the 40-metre-long system is fully automated. This means that each bar is passed through an induction coil that has been heated to around 900 degrees, before being blown off with pressurised water and then cooled. The material is then heated once again in the same machine to 650 degrees in order to achieve the appropriate strength and toughness of the required steel.”
GMH enables the construction of wind turbines with a reduced carbon footprint
The special thing about systems of this type is that they are powered by electricity. The EVA is designed in such a way that it will run on up to 100 percent green electricity. This significantly reduces the product carbon footprint (PCF) of the components manufactured in Georgsmarienhütte and the end products in which they are used. This project alone, with its associated switch from using natural gas to using (green) electricity to heat the steel, will save more than 10,000 tons of CO2 in the next ten years. For the wind power industry in particular, it is an important signal that they can also operate with a particularly low PCF in the supply chain when constructing wind farms. The launch of the EVA is yet another decisive step on the path to GMH Gruppe’s decarbonization.
In total, around 17,000 tons of steel per year can be processed by a single tempering plant at GMH. The current EVA is designed to produce smaller 20 to 60 mm bars, while planning is underway for a second, similarly designed EVA, which will produce bars from 35 to 100 mm. In total, both systems should be able to produce a total capacity of 35,000 tons of steel using electricity, by the end of 2026. This would correspond to approximately 5 percent of the total steel production at the Georgsmarienhütte plant over a year. This steel will enable the production of highly durable key parts, such as screws and fasteners for wind turbines, conveyor systems in industrial applications and steering rods in all automotive segments.
Dr Alexander Becker, CEO of GMH Gruppe, comments: ‘With single-bar tempering, we are creating the chance to open up new markets. In addition to the automotive industry, which uses our various steel grades in practically every brand and model series, the demand for hard-wearing steel grades has increased, particularly in the wind power industry. The first components from GMH Gruppe are already being supplied. As a sustainable and low-carbon production partner to this key industry, we look forward to being able to contribute further to reducing the ecological footprint of our economy by directly participating in the expansion of wind power as part of the green transformation in Germany.”
About GMH Gruppe
GMH Gruppe is a full-range supplier of recycled input material through ready-to-install components and one of the largest privately owned metalworking companies in Europe. The group comprises 15 medium-sized production companies in the steel, forging and casting industry and is present in more than 50 countries. With around 6,000 employees, the GMH Gruppe generates annual sales of around two billion euros. GMH Gruppe is a pioneer in sustainable steel production and has also been accepted into the “Association of Climate Protection Companies”. By recycling scrap metal, the company produces green steel and thus makes an important contribution to the circular economy. The use of electric arc furnaces at four of its sites reduces carbon dioxide emissions by a factor of five compared with conventional blast furnaces. This, in turn, also reduces the carbon footprint of GMH’s customers. Global customers include companies from the automotive industry, mechanical and plant engineering, railroad technology, power generation, transport logistics as well as the sectors, aerospace, agriculture and construction machinery. The GMH Gruppe has set itself the goal of being completely climate-neutral by 2039.
About Georgsmarienhütte
Georgsmarienhütte GmbH, based in Georgsmarienhütte, Lower Saxony, is a leading European supplier of crude steel, steel bars and bright bars based on quality and engineering steels. In addition, the company supplies machined and ready-to-install components. Already today, Georgsmarienhütte is one of the most climate-friendly steel companies in Germany. With its comparatively low-CO2 value chain, which consists of melting scrap in the electric arc furnace and recycling it into new steel, the company is a pioneer in sustainable steel production, making an important contribution to the circular economy. The methodology used by Georgsmarienhütte to calculate its Product Carbon Footprint (PCF) has been validated by TÜV SÜD and is now being applied to more than a thousand steel variants. Besides the automotive industry and its suppliers, Georgsmarienhütte serves customers in the mechanical and plant engineering and energy industry. Steel made in Georgsmarienhütte is used where exceptional stresses have to be coped with, where power is generated and immense forces have to be transmitted, and where safe and wear-resistant operation is essential.
For inquiries
GMH Gruppe
Luciana Filizzola
Director Sustainability and Communications
bmb-consult – PR-Agentur der GMH Gruppe
Simone Boehringer
Senior Editor & Senior Account Manager