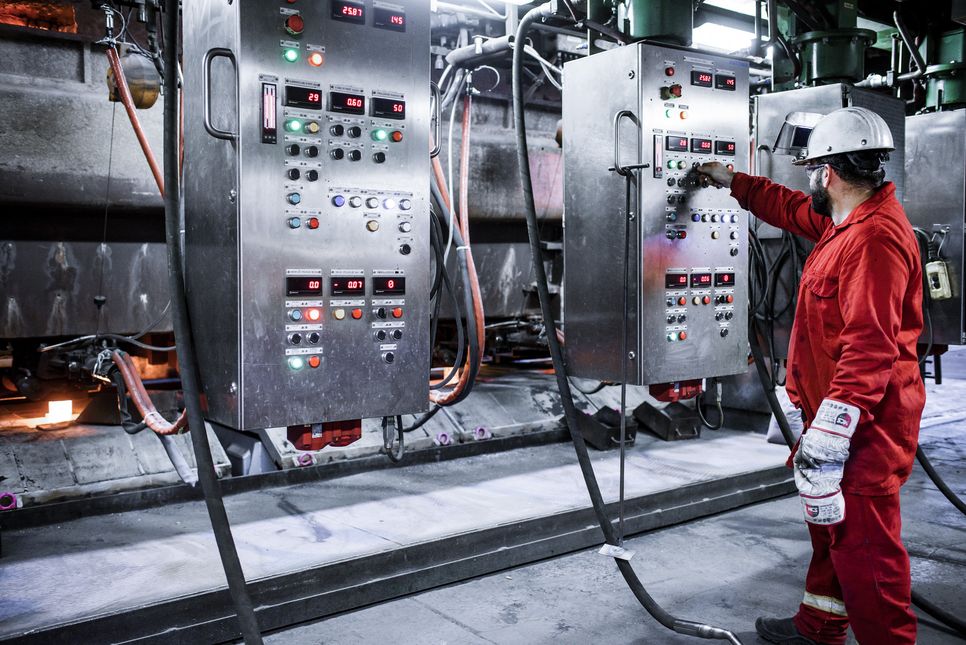
Bainitic steel – for significant savings potentials
Bainitic steels combine the optimum properties of quenched and tempered (QT) steels with the short production routes of PHFP steels. This fact makes steels like Georgsmarienhütte GmbH’s 16MnCrV7-7 (H2), 1.8195 the ideal steel for structural components in automotive engineering: assured versatility at rational cost.
The automotive industry makes demands that are well above average on its steel. Here, microalloyed air-hardening bainitic steels such as 16MnCrV7-7 (H2), 1.8195 meet expectations that cannot be fulfilled by PHFP or quenched and tempered (QT) steels alone.
These steels incorporate the excellent mechanical properties of quenched and tempered steels but require only the short process times of PHFP steels. Combination with optimum alloying concepts makes it possible to save up to 30% of costs compared to a QT steel such as 42CrMo4.
The benefits of 16MnCrV7-7 (H2), 1.8195:
- Optimum mechanical properties combined with high strength, thanks to the steel's fine bainitic microstructure
- High savings potentials thanks to short process times and rational-cost alloying concepts
- Suitable for lightweighting (lightweight engineering), case hardening and carbonitriding
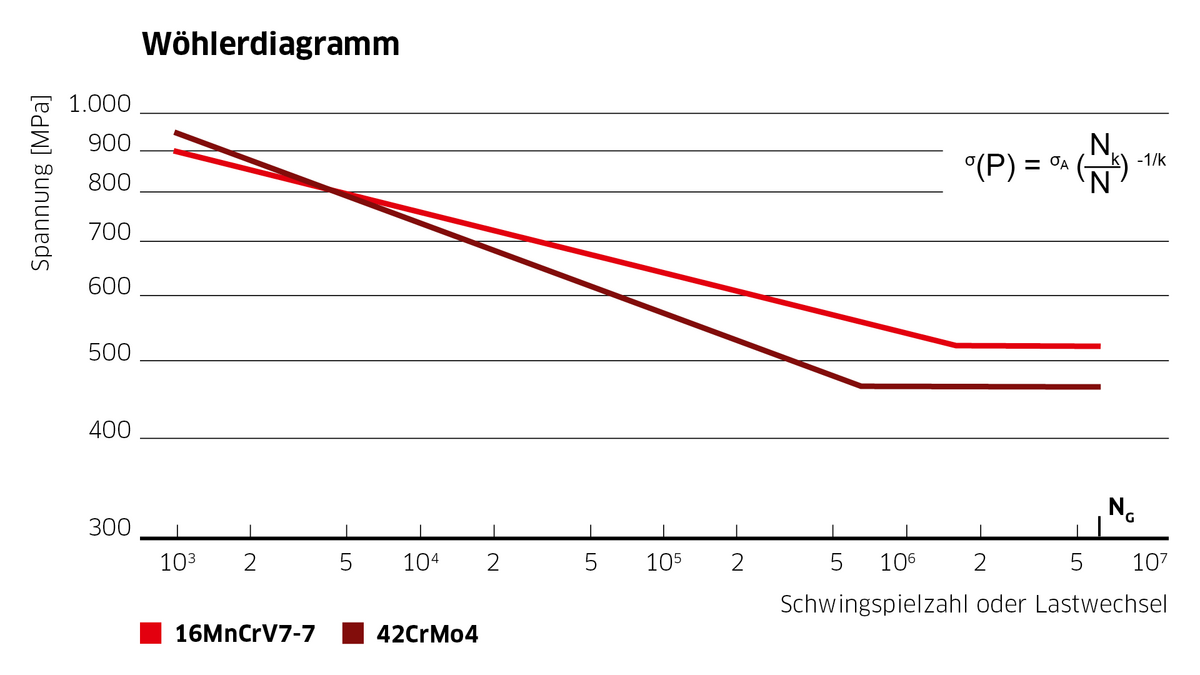
Bainitic steel: a material with the optimum microstructure
Many applications demand the use of hard, high-strength steels. Our bainitic 16MnCrV7-7 delivers convincing arguments in the tensile and Charpy V-notch toughness tests: its test data are within the range achieved by a 42CrMo4 quenched and tempered steel.
Fatigue-strength analyses actually indicate better dynamic properties than in the latter steel. The good mechanical properties of 16MnCrV7-7 are systematically imparted: continuous cooling takes place by means of optimised temperature control from forging heat. Still more benefits accrue from this material’s fine bainitic microstructure.
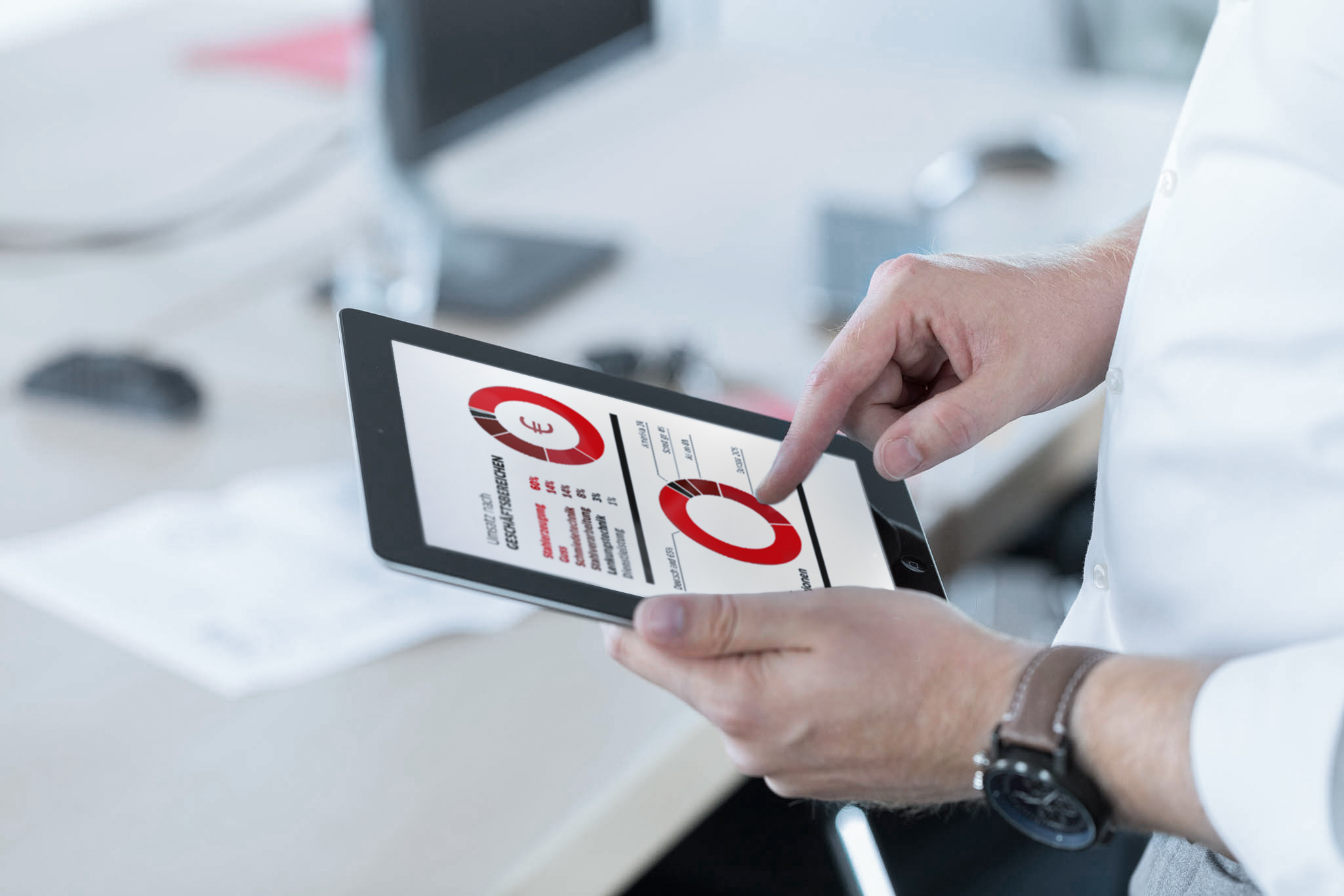
30 Prozent
lower production costs compared to a 42CrMo4 quenched and tempered steel are possible for forged components (example: common-rail diesel fuel-injection components)
Shorter processes, better alloys
It proved possible to save around 30 percent of production costs compared to the quenched and tempered 42CrMo4 steel when using 16MnCrV7-7 for the production of a forged common-rail component for diesel fuel-injection systems. The reasons for this can be found, above all, in the fact that there is no need for quenching and tempering, crack inspection or straightening when bainitic steels are used.
Costs reductions are also achieved thanks to the cost-optimised alloying concept employed: high-cost volatile alloying elements such as molybdenum and nickel are excluded. This steel, developed jointly by Georgsmarienhütte GmbH and a major customer, forms the basis for mass production of injectors and common rails.
Steel with far-reaching potentials and perspectives
Case hardening and surface carburising, along with lightweight engineering, are among other applications for microalloyed air-hardening bainitic steels. Tests performed using 16MnCrV7-7 (H2carb) steel have already demonstrated that its properties are comparable to those of 18CrNiMo7-6 – but with even lower production costs. Here, the reasons can be found, above all, in the steel’s high potential hardness increase and fine-grain stability, which also further shorten the production process.