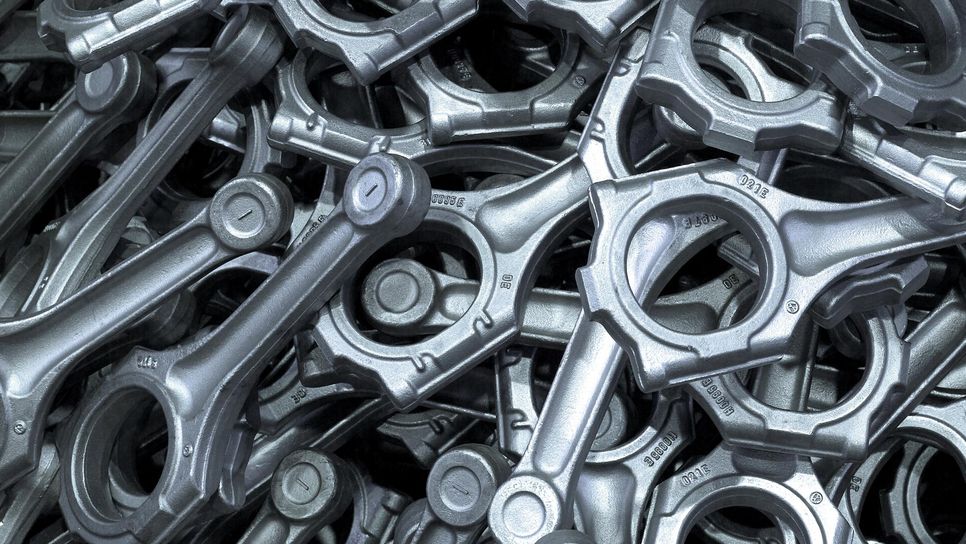
Boosting the strength of PHFP steels
GMH Gruppe has long been the reliable partner of the automotive industry. Our con-rod steels, for example, are noted for their high mechanical strength and excellent crackability. Despite these high achievements, our development teams saw no reason to rest on their laurels: a new generation of even further enhanced steels is already available.
How it all began: 1992 saw the birth of steel C70S6, the first ever fracture-splittable forged steel. That steel was developed by Georgsmarienhütte GmbH in a joint project with other companies. Before the development of C70S6, connecting rods were made of steels that deformed upon fracture splitting, due to their high ductility. C7026, in contrast, exhibited precisely mating fracture surfaces. In addition, the steel possessed good machining properties combined with high mechanical and yield strengths.
The yield strength indicates the stress at which a material begins to deform plastically, i.e. irreversibly. Prior to the yield strength, the material will deform elastically and return to its original shape once the applied stress is removed. A material’s yield strength is determined in tensile tests in which the material is subjected to a uniaxial, torque-free tensile force. The yield strength – sometimes called the yield point – of a material is an important parameter, not least of all in connecting rods, which are subjected to extremely high compressive and tensile stresses in engines – an extremely demanding application that requires steels with excellent high-strength properties.
The benefits of fracture-splittable PHFP steels:
- No quenching and tempering needed
- No machining of the split surfaces
- Much less big end and small end machining
- Ultra-reliable performance under extreme in-service stresses
The next stages of development
In the automotive industry, we have recently been witnessing a growing trend towards more powerful and more efficient engines, and with this trend grew the performance requirements on con-rod steels. From C70S6 we developed our 70MnVS4 grade which, thanks to its higher manganese and vanadium contents, forms fine precipitate particles. These result in significantly improved strength properties. 70MnVS4 has been used for many years by various European engine producers for the manufacture of connecting rods subjected to elevated in-service stresses.
In 2010, Georgsmarienhütte developed the 46MnVS5 steel and its variant 46MnVS6 mod. This steel contains niobium as an additional alloying element. Niobium provides excellent strength values, making this steel a highly suitable material for efficient lightweighting solutions: 46MnVS5 connecting rods weigh ten percent less than connecting rods made in C70S6. 46MnVS5 has now become a standard feature of customer and product specifications worldwide.
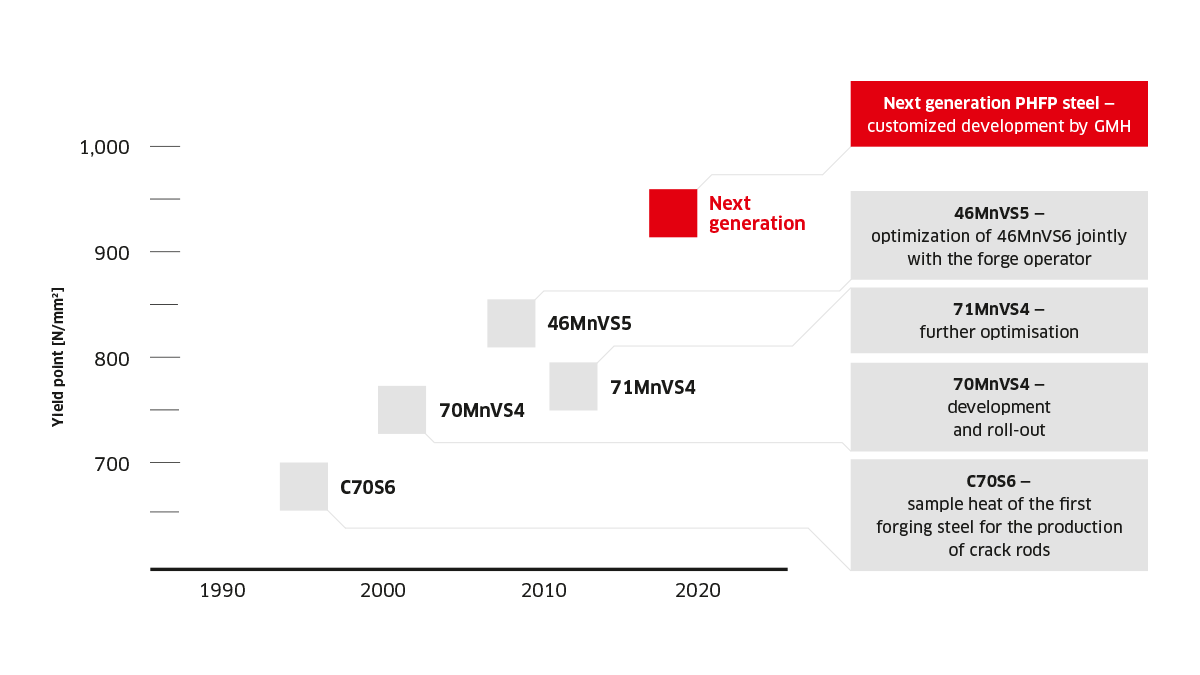
The next generation is ready to go
Future mobility will require increasingly sophisticated solutions. Vehicles will have to become lighter and more efficient in order to cut emissions – but with no compromises on safety. In a cooperation project with one of our customers, we have developed the next generation of fracture-splittable PHFP steels. These possess yield strengths of 850 MPa or more – significantly higher than previously available PHFP grades. This enables us to supply the perfect steel for fracture-splittable connecting rods that will also meet with certainty the growing requirements of the future: high-efficiency lightweighting, excellent resistance to mechanical and other stresses, and optimum workability.