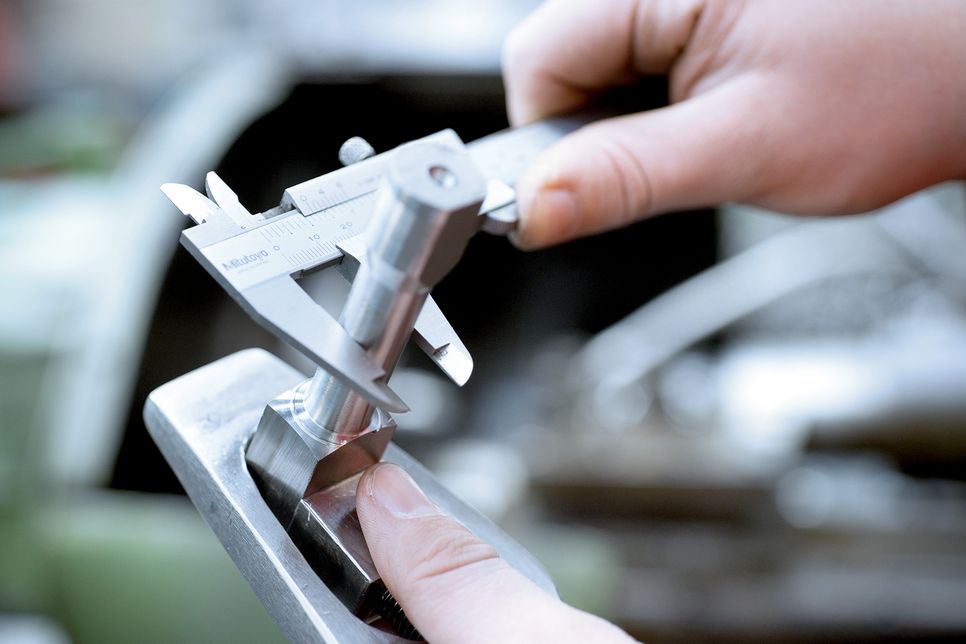
High-alloy, high-precision
Energietechnik Essen GmbH’s Cronidur 30 high-nitrogen steel (HNS) is exceptionally mechanically strong, hard and corrosion-resistant. We produce it using the world’s currently largest PESR system in processing sequences that are precisely tailored to each other and interlink the capabilities of multiple GMH Gruppe companies.
Along with our P2000, HNS 28 MP and a number of other grades, Cronidur 30 is one of the high-nitrogen steels (HNS) in Energietechnik Essen GmbH’s range. It is, without the slightest doubt, a particularly high-tech product and necessitates special precision in its production and further optimisation to accommodate every individual customer requirement.
Precision in production of Cronidur 30
- Optimum cooperation between Energietechnik Essen, Schmiedewerke Gröditz and Geissler Wista
- Precise attainment of the mechanical properties demanded by the customer in quenched-and-tempered state
- Precise harmonisation of austenitisation and tempering temperatures and the quenching fluid used
Optimised synergies
Precision in the production of our high-nitrogen steels starts as early as the well-practised cooperation between multiple group companies: on the basis of a detailed chemical-composition specification entailing special limits for the ingot-casting process, Schmiedewerke Gröditz supplies the precise customised feed material. Remelting, refining and nitrogen-alloying then take place at ETE, while Geissler Wista specialises in the peeling of quenched-and-tempered bars of this mechanical-strength level.
Precisely adjusted properties
Detailed knowledge of material behaviour during heat treatment makes possible precise fulfilment of customers’ wishes in terms of mechanical properties in quenched-and-tempered state. Ultra-precise on-spec results are also attained via the optimum matching of austenitisation and tempering temperatures and precise selection and preparation of the quenching fluid. We are thus able, in the field of martensitic steel variants, to supply high-performance products with mechanical strengths extending up to 1750 MPa.
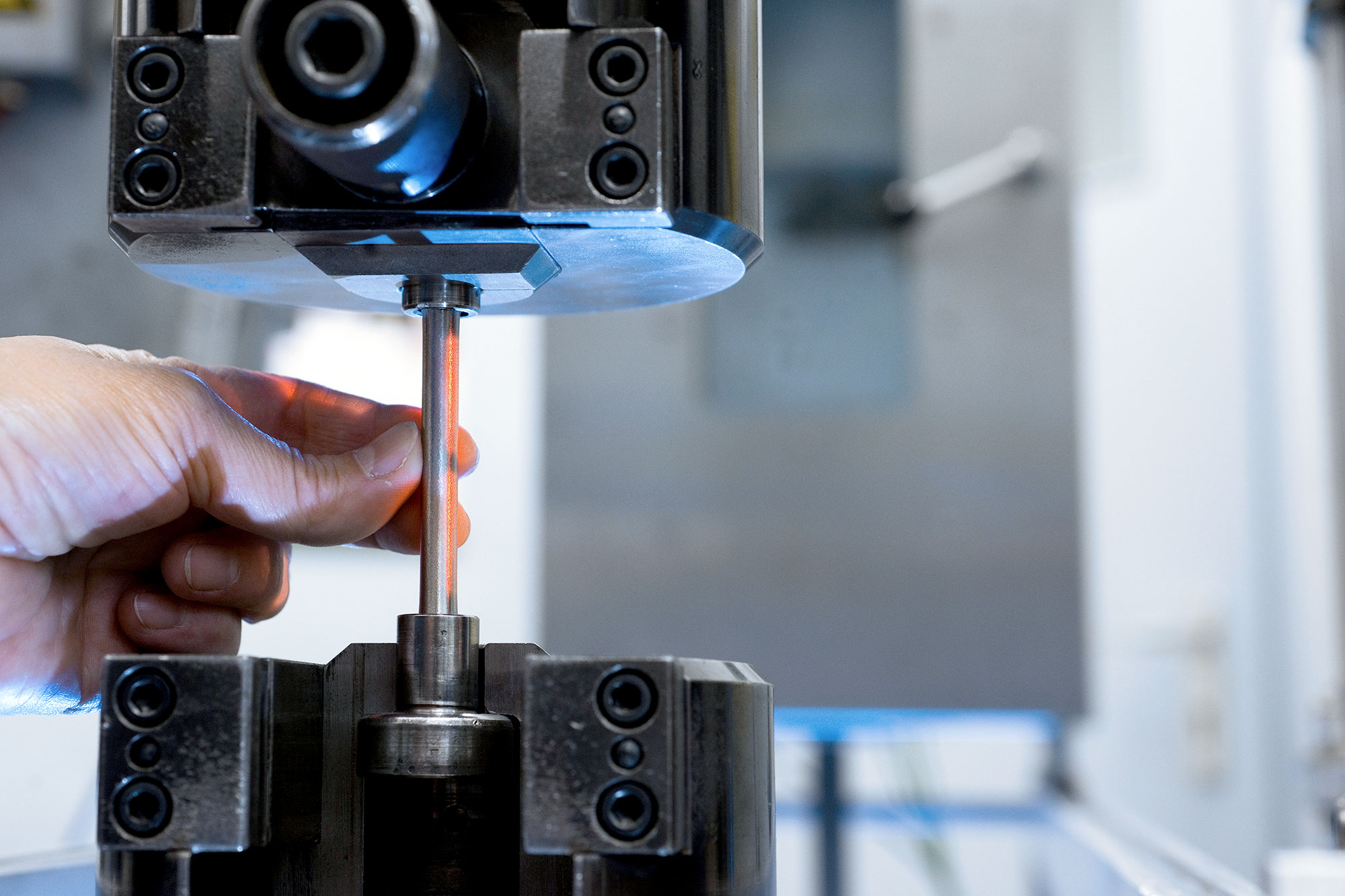
25 PREN
Our martensitic steels exhibit exceptionally high corrosion resistance, achieving PREN data of up to 25.
The world’s largest PESR system
The feed material is refined, nitrogen-alloyed and transformed into Cronidur 30 in the world’s currently largest PESR system (status: April 2021). This permits alloying of especially high nitrogen contents in austenitic and martensitic steels while nonetheless maintaining ultra-tight tolerances for all remelting parameters. This enables us to generate technological properties that go well beyond the capabilities of standard materials.
Our martensitic steels
Our martensitic steels (MHNS) achieve exceptionally high corrosion resistance levels, with PREN data of up to 25. In addition, their hardnesses of up to 60 HRc mean that they are extremely resistant to rolling-contact fatigue. Our HNS 28 MP also forms part of this materials group, in addition to Cronidur 30.
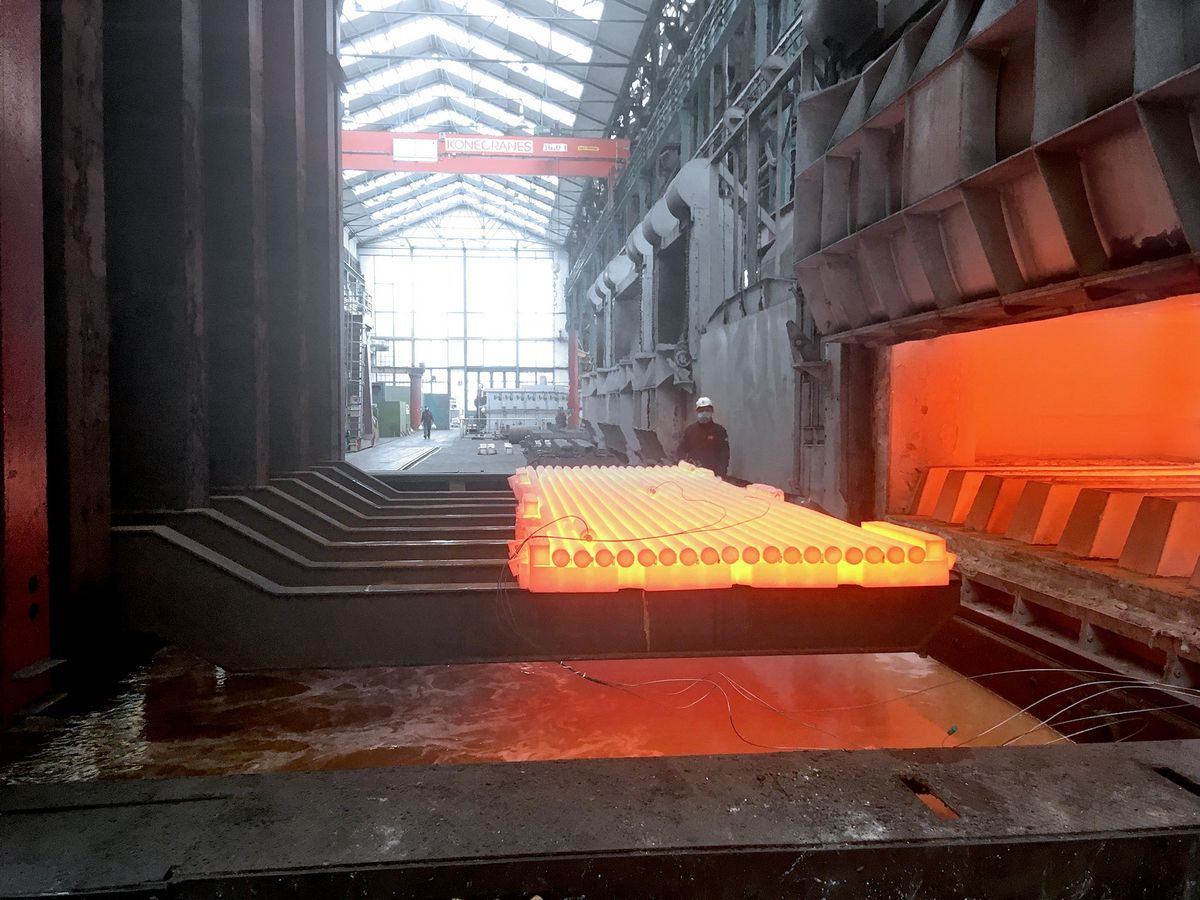
Our austenitic steels
Among the austenitic steels (AHNS), our nickel-free material P2000 convinces in particular with its ultra-high corrosion resistance combined with extremely good mechanical properties. Even in solution-annealed state, it achieves a yield strength of 600 MPa. Its resistance to wear can be compared to that of manganese steel. With PREN data of up to 48, it is so corrosion resistant that it is customarily used in fields such as oil and gas production, and also in medical applications.
Multidimensional potentials
Here at Energietechnik Essen GmbH, we frequently produce bar lengths of up to 6000 mm, and even larger dimensions are possible. We cooperate closely with external partners to assure these potentials. Heat-treatment operations performed away from our plant are supervised by our experienced tempering and quenching specialists in the field of HNS grades. With Cronidur 30, quenching and tempering is, for us, a never-ending learning curve that enables us to continuously optimise even further the very high precision we already achieve.