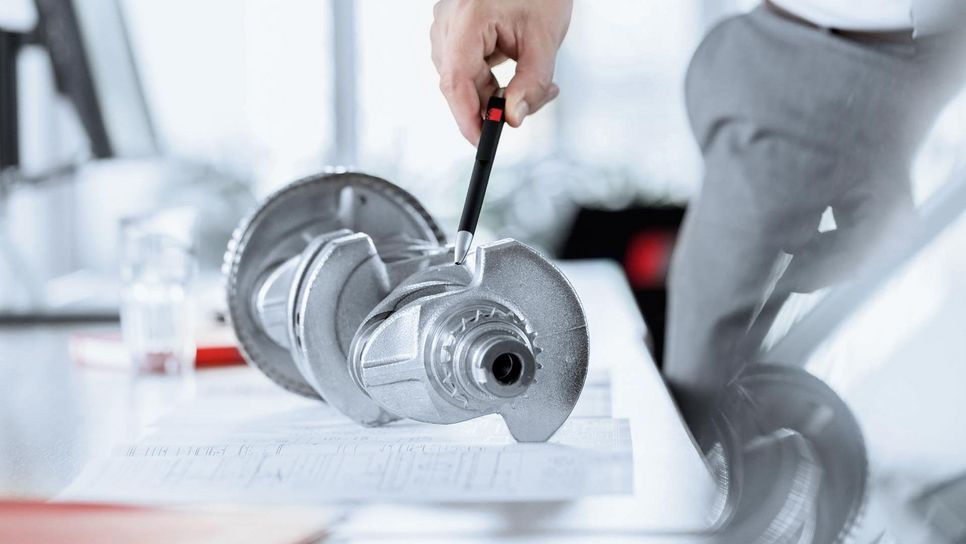
High-strength steels with high energy efficiency
The introduction of the EEG (German Renewable Energy Sources Act) surcharge has significantly increased the pressure for the industry to become more energy-efficient. Working closely with our customers in the automotive industry, we have developed two new steels that will play a significant role in saving energy. In turn, these have provided a platform on which we have been able to come up with new concepts for energy-efficient, cost-effective process routes.
Thanks to our cutting-edge production technology, we can produce steel materials that are tailored to the exact requirements of our individual customers. This is our greatest strength, and it enables GMH Gruppe to play a key role in energy-efficient steel production.
New development 1: efficient manufacturing, impressive properties
Precipitation-hardened steels, such as AFP steels, acquire their mechanical properties directly from the forging process. The components are subjected to a regulated cooling process as soon as they leave the heat of the forge. There is no need for any subsequent heat treatment, which reduces process costs. Component straightening and the associated crack inspection process are often also rendered superfluous. These steels, however, have a lower yield strength and notch impact energy than quenched and tempered steels. Georgsmarienhütte GmbH’s newly developed, bainitic forged steel 16MnCrV7-7 (1.8195) offers the same advantages as both precipitation-hardened AFP steels and any quenched and tempered steel. This means that it requires only short process times while still offering excellent mechanical properties. It also follows a cost-effective alloying concept that does not use expensive or volatile elements such as molybdenum or nickel.
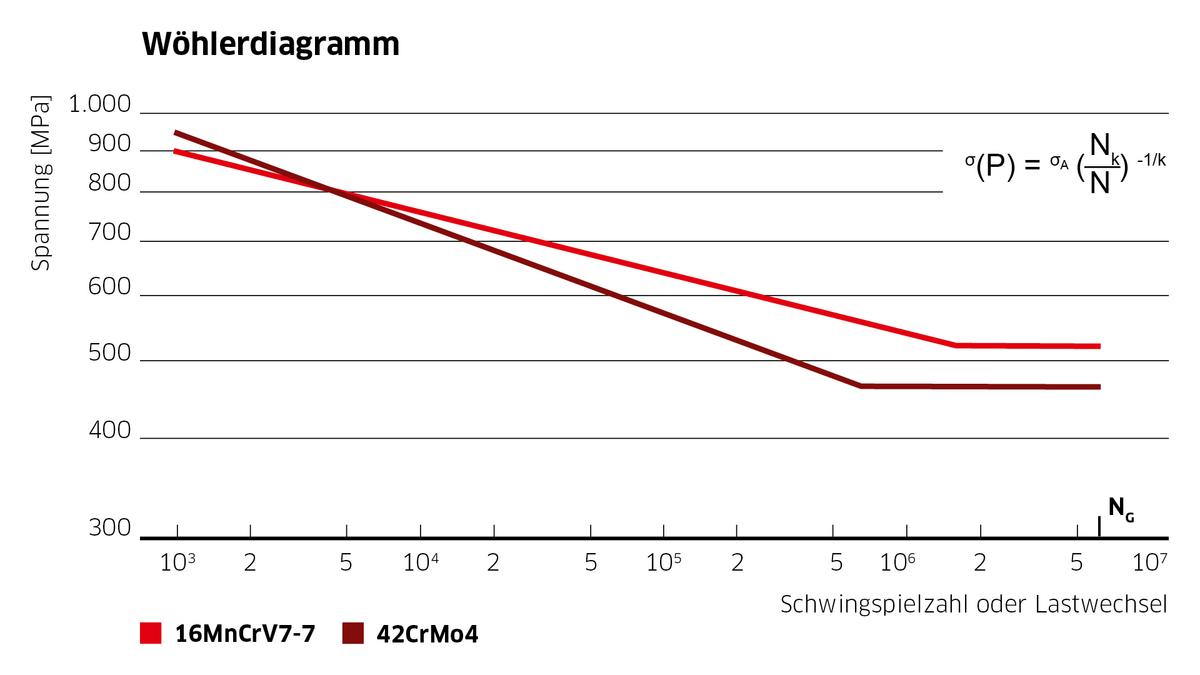
New development 2: lower costs, higher core strength
Inductive hardening plants are known for their compact design. This enables them to be incorporated directly into the production process, thus allowing for single-piece flow – with lower investment costs and much shorter batch lead times. Our new steel 50CrMnB5-3 (1.7136) has a low carbon content, and combines the benefits of warm working and subsequent inductive hardening. Once it has been forged and subjected to controlled air cooling, it demonstrates a high core strength and an optimum pearlitic microstructure. The forged parts can then be inductively hardened without any problem.
Combining the qualities of existing materials and processes to produce innovative new solutions – this kind of progress in terms of efficiency and energy-saving is what makes GMH Gruppe steels the materials of the future.