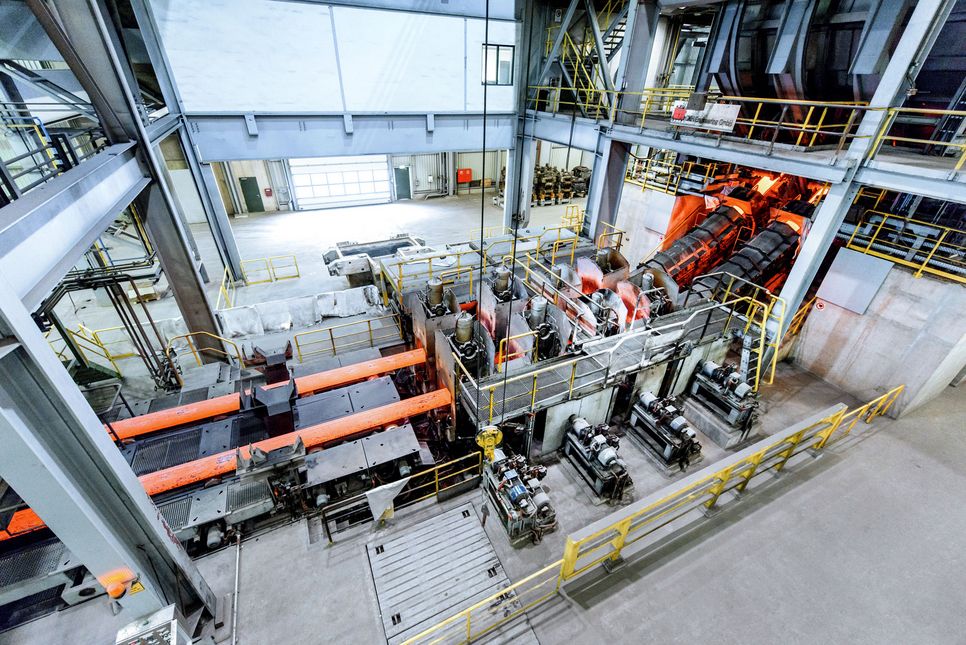
Stahlwerk Bous: New filter installation
A truly groundbreaking, future-oriented investment – the new dust-extraction system at Stahlwerk Bous GmbH boosts steel production and protects the environment simultaneously. Not only is the exhaust air released by the steelworks now five times cleaner than required by the applicable environmental law – steel output from the Bous AC EAF (electric arc furnace) has also increased significantly since the installation of the new filter system.
The new filter installation at Stahlwerk Bous GmbH proves conclusively that high-grade steels can be produced in Germany with only minimal impact on the environment. An extraordinarily effective filtering process reduces the dust content of the waste gas from the steelmaking process to just 1 milligram per cubic meter. As a comparison: the legally binding limit is 5 milligrams per cubic meter!
With its throughput of 1.3 million cubic meters of waste air per hour, this new technology assures enormous improvements both for the environment – thanks to the much higher filtration rate compared to the previous equipment (only 560,000 cubic meters per hour) – and for GMH Gruppe’s Stahlwerk Bous, which has been able to dramatically raise output to 70 tonnes of steel per heat since the installation of the new dedusting system.
Benefits of the new dust-extraction and filter system:
- Dust content in the waste air released is now five times lower than the legal limit
- Higher steel output
- Economic and environmental improvements that help to assure the future of Bous as a steelmaking location
New technology generates important benefits
The groundbreaking concept of the new filter system makes it one of the most advanced installations of its kind in the world. Combustion of the flue gases from the EAF in a post-combustion chamber, for example, completely destroys the pollutants contained in the gas. The hot gas is then immediately quenched with cold air.
This optimally designed and, at the same time, eco-friendly routing of the gases from the extraction to the release points was defined in comprehensive CFD simulations. Flow-optimised routing of the gas also ensures that pressure drop is ultra-low and that energy consumption for the fans is reduced to the technically feasible minimum.
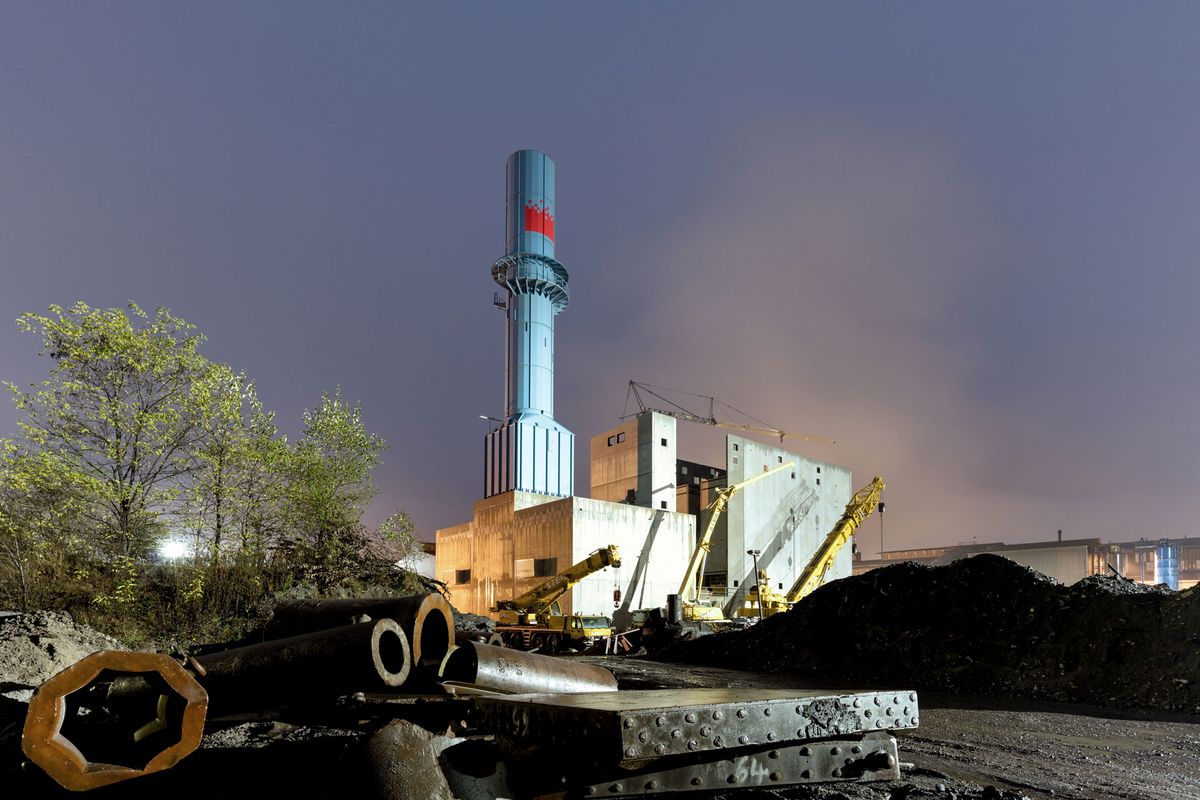
5 times
cleaner than required by law: the ultra-clean waste gas filtered at Bous.
Total redesign
Bous as a steelmaking location also benefits directly from the new filter technology. Apart from the fact that the two-digit million euro investment sends an unequivocal signal to the region that Stahlwerk Bous has a secure future, other positive effects include a better workplace environment thanks to the significantly improved dedusting performance of the new filter system. In addition, the heat recovered from the extracted air is now fed back into the plant’s district heating system, while the new filter house, constructed from pre-cast concrete, ensures highly efficient thermal and acoustic insulation of the filtration process.
Stahlwerk Bous GmbH had to solve a number of engineering challenges to permit the implementation of the best possible solution. A sophisticated structural design concept was drafted in order to accommodate the much bigger suction hood above the furnace and the enormous waste-gas ducts with their diameters of up to 4.3 m. Today, a 50-m-long and up to 20-m-wide steel gantry bears the weight of the new dust-extraction equipment – a real heavyweight in assuring future-safe steel production.
The system in operation: constantly updated data
Stahlwerk Bous GmbH publishes the 24h averages for dust content measured in the filtered waste air on its websites. This data is updated every day and is freely available to the public.
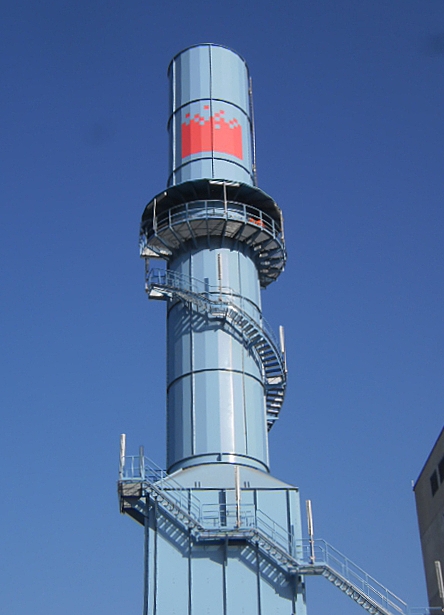