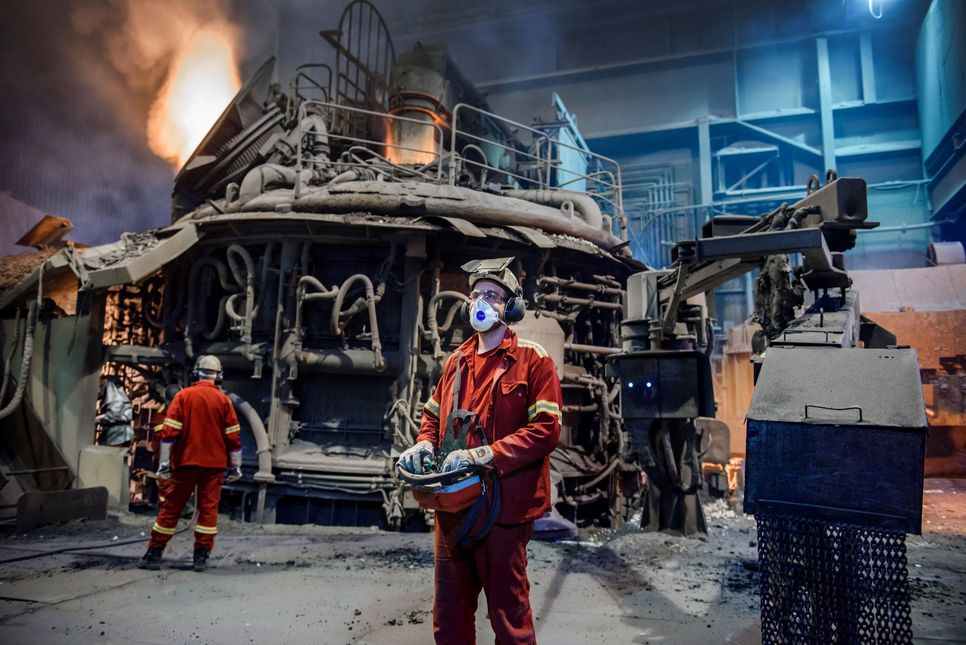
The electric arc furnace: New directions
The electric arc furnace (EAF) is the central element in steelmaking at Georgsmarienhütte GmbH – in exactly the way that improvements to processes and technologies are a central topic within the GMH group. When these two meet, the results are things, such as an innovative waste-gas routing, that improve even further tried-and-tested facilities such as our furnace.
The melting of scrap in an electric arc furnace to make steel inevitably results in the necessity for cleaning and repair work. This, as is well known, costs both time and money. A new design for the EAF’s waste-gas system assists in significant savings of both. And even more: the improved EAF also benefits safety at the workplace. The core of this improvement project can be found in the system’s new waste-gas arrangement.
Benefits of the new furnace design:
- Automatic elimination of depositions
- Relatively low production and cost input
- Reduced cleaning and repair needs
Simulation of flow in the electric arc furnace
Many routes can lead to the target. Which of them is the best, is something we do not leave to chance, but instead, for example, to ultra-accurate numerical fluid mechanics. With this assistance, our design experts were able to calculate from sixteen conceptual variants the best solution for future waste-gas routing in the electric arc furnace – quickly and at rational cost. In the end, it was apparent: a larger cross-section for the post-combustion chamber and the exhaust pipe connection were the key to success. In addition, the thermal load on the furnace walls during steelmaking using scrap was determined in the context of a final simulation. This made it possible to specify the optimum design for cooling of the EAF.
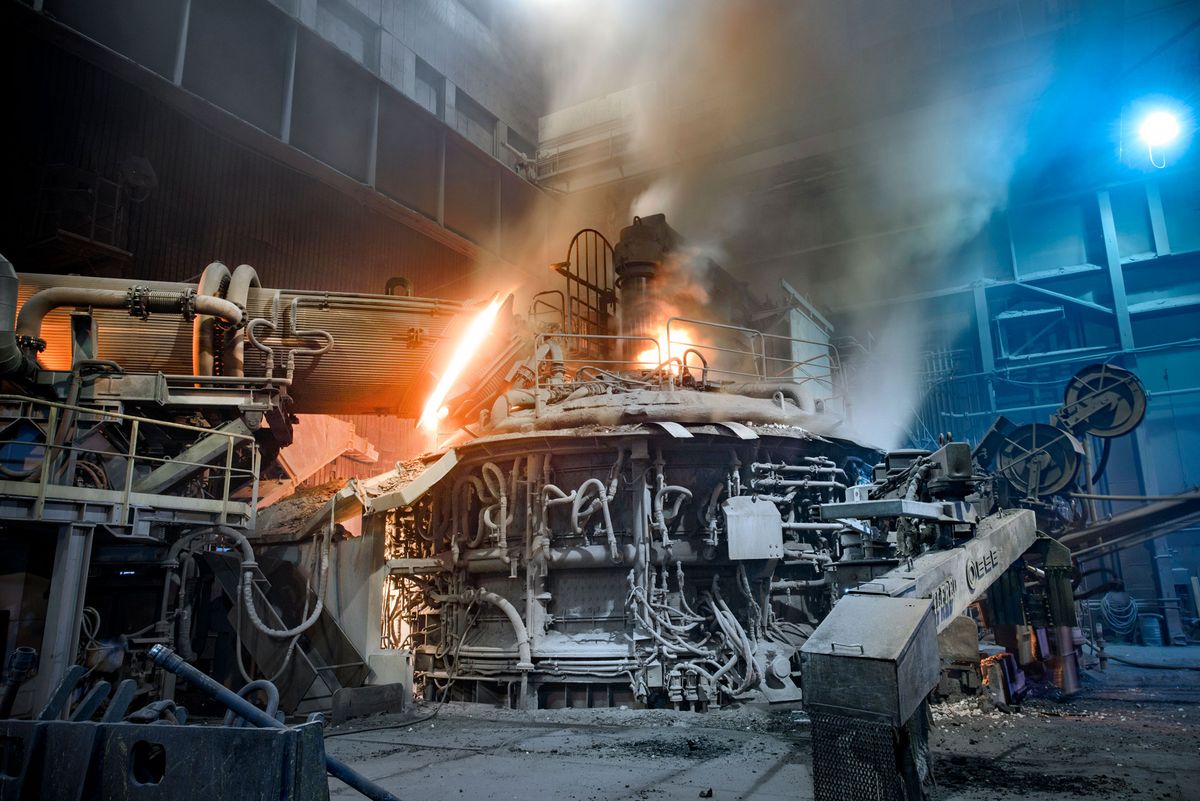
16 Varianten were submitted by our experts to exhaustive simulation. Finally, a design variant that had already proven its worth in practice was selected.
Waste-gas routing in the electric arc furnace
The new waste-gas arrangement for the electric arc furnace at the Georgsmarienhütte GmbH steel mill fulfils the promise of the simulation. Waste gases generated during the production of steel are captured extremely efficiently. Depositions in the furnace’s waste-gas system are, as predicted by the simulation, automatically removed by means of a continuous self-cleaning mechanism.
This is assured by a straight waste-gas route between the electric arc furnace and the post-combustion chamber. In addition, the waste-gas pipe is now positioned sloping in the post-combustion chamber during tapping, with the result that potential depositions simply drop out of the pipe by gravity.