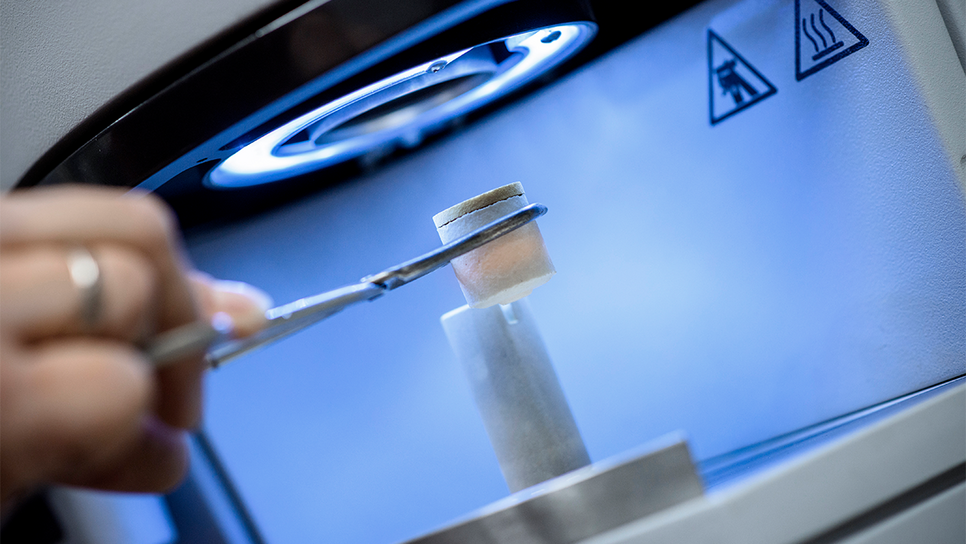
The right steel for every challenge
Lightness and high-strength in one and the same material. Highly durable under extreme in-service stresses. Outstanding efficiency thanks to short process chains. Exactly the right blend of alloying elements, combined with the matching technology, enable us to create steels that meet every need in every application When international standards do not provide the perfect steel grade or steel variant for your application, we develop a new one specifically for you.
Georgmarienhütte GmbH’s range of steels includes more than 500 different grades. But customer requirements can be so diverse, and new applications are sometimes so specialised, that, even with our vast range of existing grades we need to find new ways of meeting our customers’ requirements 100 percent. This is where our team of technologists and materials development specialists come in: they will work closely with the customer to modify an existing steel to the new requirements – or to develop a totally new grade.
By adding alloying elements – chromium, nickel, molybdenum and manganese, for example – and microalloying elements – such as niobium, vanadium and titanium – in precisely adjusted amounts to the steel heat and employing material-specific production and processing methods, our experts create materials that incorporate exactly the properties needed for the specific application – exclusively for the individual customer. All stages of such projects – from initial consultation, via the development of a specific concept, up to and including roll-out – are carefully customised, resulting in a material perfectly suited to fulfil even the most exacting requirements made on critical components in vehicles, high-capacity power generators and chain conveyors in the mining industry.
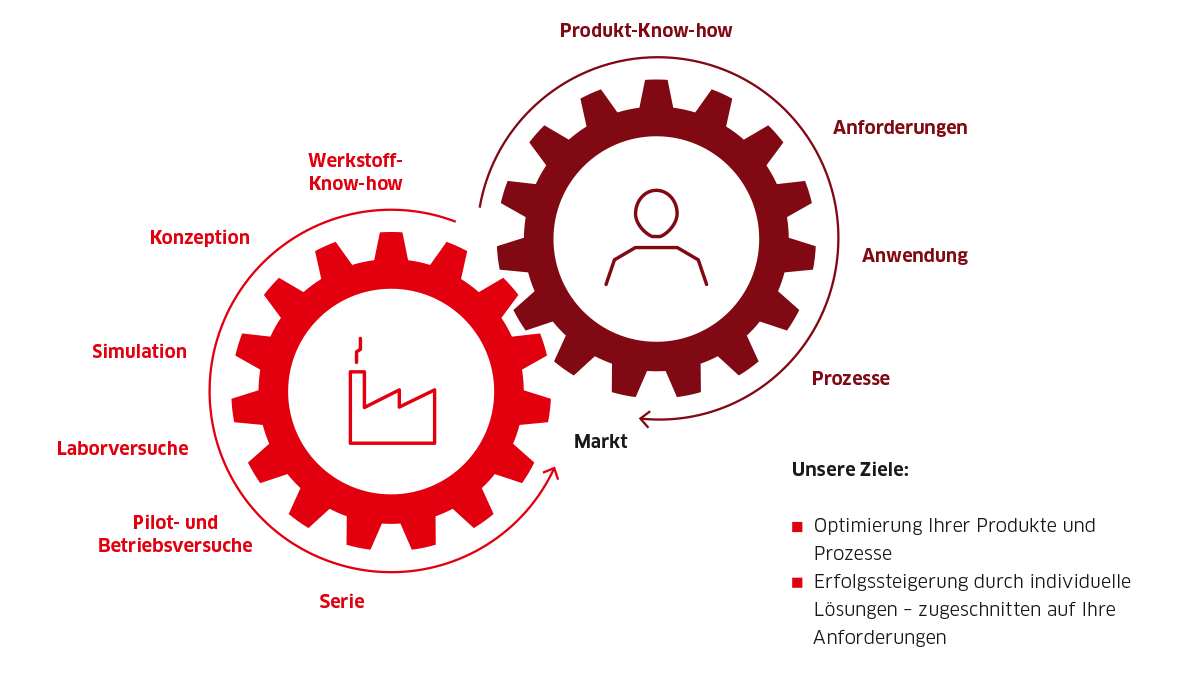
The benefits of customised steels:
- Cost reduction for the customer and lower emissions along the entire production chain, thanks to optimised process efficiency and shorter processing cycles
- A smaller CO2 footprint enabled by lower-weight components helps protect the climate and the environment
- Components made in customised steels are more durable and withstand higher in-service stresses, promoting future technologies such as electromobility
- A wide range of sectors benefit from optimum manufacturing materials
Innovative materials concepts assure optimum steel properties
Thanks to a special alloying technology, bainitic steels, such as our 16MnCrV7-7 (H2), 1.8195, combine the benefits of two steel concepts in a single material: the excellent mechanical properties of quenched-and-tempered grades and the short production cycles of PHFP steels. The end result: a high-strength steel that can reduce your production costs.
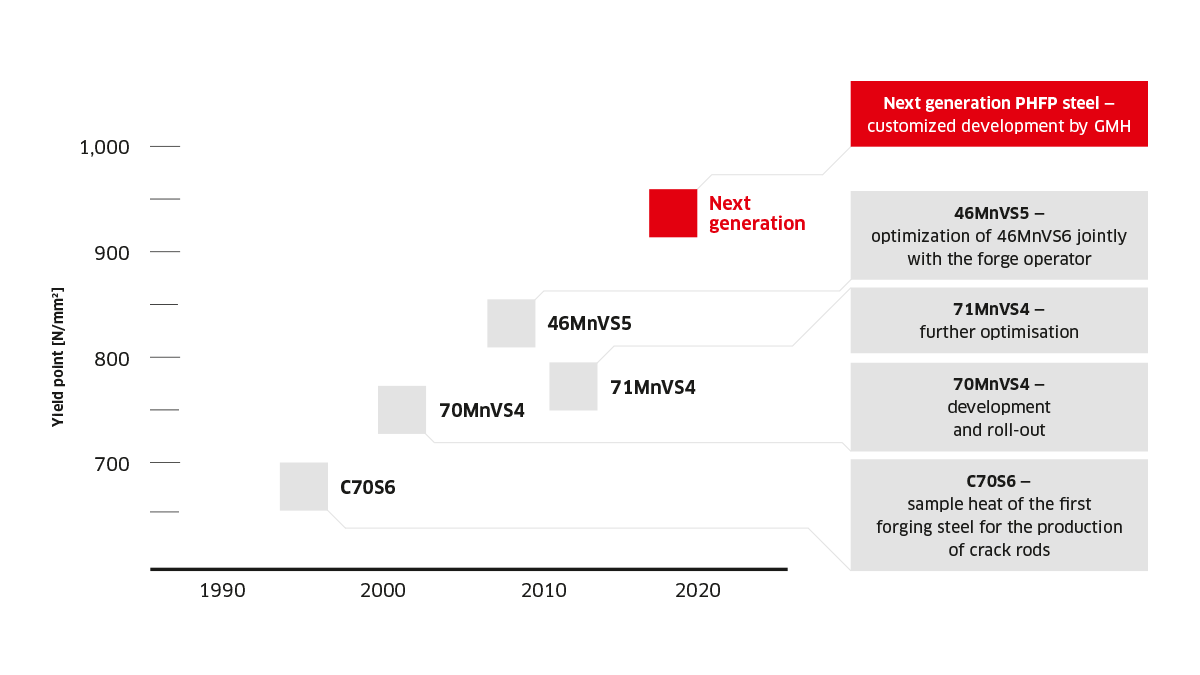
High strength, low weight
Our PHFP variant 46MnVS5 also incorporates numerous outstanding innovative properties. Thanks to the high strength of this steel, 46MnVS5 components require less material to achieve equivalent performance – while simultaneously reducing the component’s weight. These unique features make this steel a material with enormous lightweighting potential. As if this were not enough, our development experts additionally increased this steel’s yield strength to above 850 MPa, making it an even more promising candidate for lightweighting – as demonstrated by our next-generation fracture-splittable con-rod steel, which is currently in the prototyping phase.
We also continuously research into the improvement of fine-grain stability, a factor essential in assuring good machinability and excellent mechanical properties in a steel. In numerous joint projects with customers, we have successfully optimised a wide range of case-hardening steels and related process parameters along the process chain – up to and including the case-hardening process itself. Users report that these steels score with their extraordinarily high fine-grain stability. These, and the other fine-grain stabilised case-hardening steels suitable for high-temperature carburizing that we supply, enable our customers to produce components in steel with maximum efficiency.
We share our experience with a range of research institutes, such as the Arbeitsgemeinschaft Wärmebehandlung und Werkstofftechnik e. V. and Forschungsvereinigung Antriebstechnik e. V. in order to promote innovation in this field of steelmaking. In this way, we make an important contribution to the development today of the steels of tomorrow.