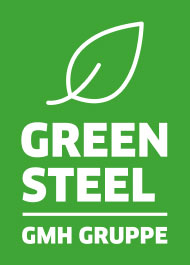
Green Steel for
a sustainable future
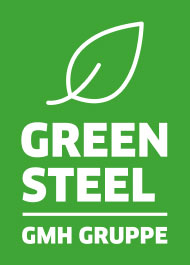
We are Green Steel
80% lower
CO2 emissions
Almost 100%
recycled material
We are pioneers in the production of steel that emits 80 percent less CO2 than conventionally produced steel. In our state-of-the-art electric furnaces, we use almost 100 percent scrap metal to produce top-quality steel. We have been relying on this trailblazing technology for decades – and are constantly developing it further.
For a future worth living
We will always
be a green steel pioneer
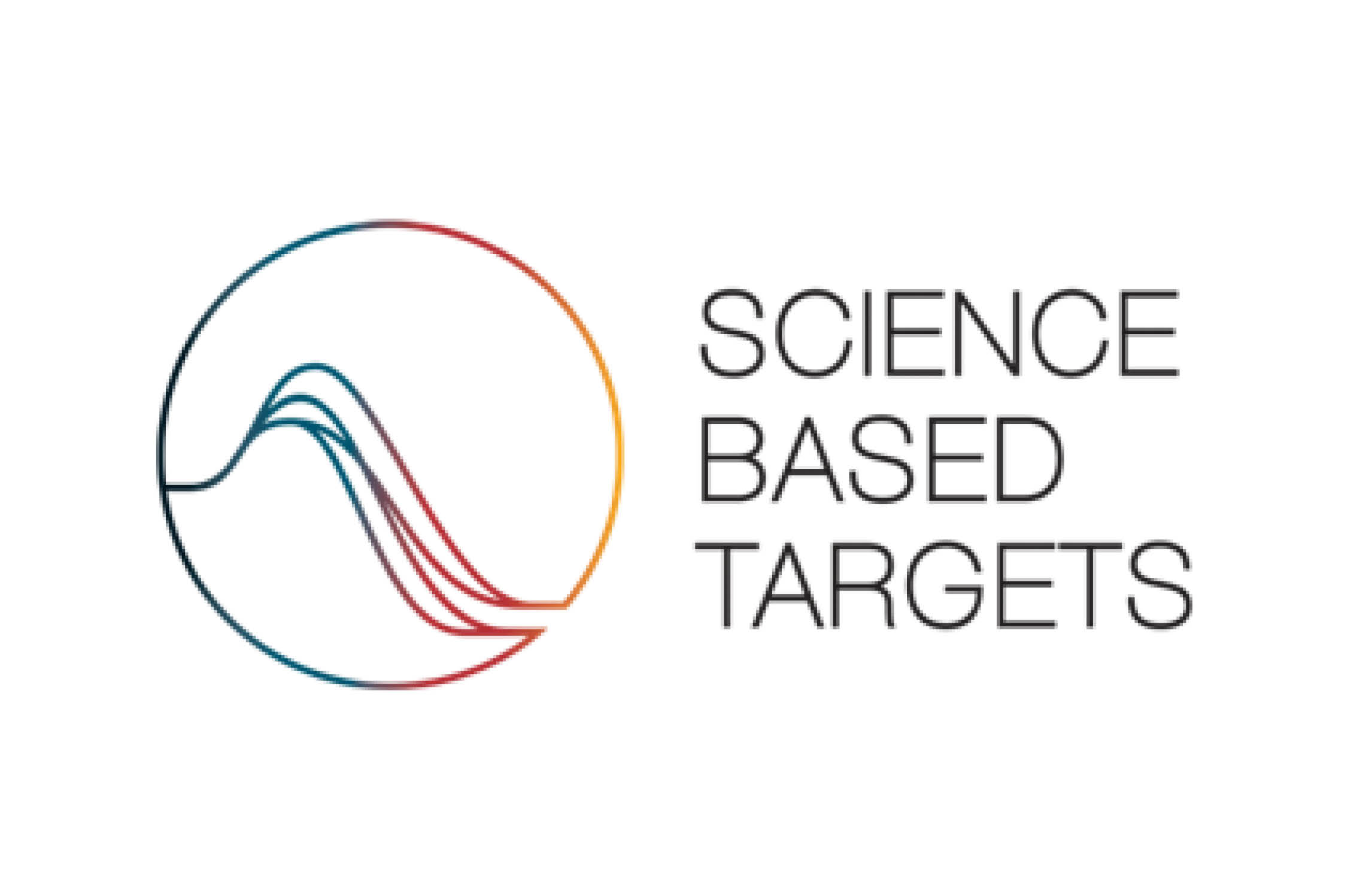
Science-based climate protection
in line with the Paris Agreement
We have joined the Science Based Targets Initiative (SBTi) and have our climate targets scientifically validated. This means we are committed to a transparent and measurable reduction in our CO₂ emissions – in line with the Paris Climate Agreement. Our goal: climate-neutral steel by 2039. By using green electricity, hydrogen-capable production processes and a sustainable supply chain, we are actively driving the transition to a climate-friendly industry. Click here for the press release.
Green steel as a stepping stone
to a sustainable future
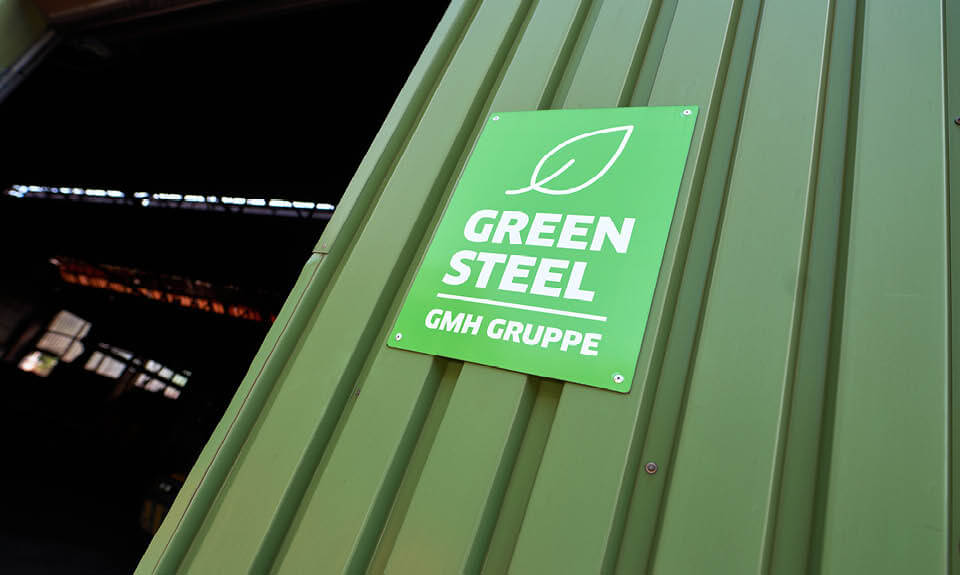
Steel production is responsible for around nine percent of man-made carbon emissions worldwide. We take this responsibility seriously. Thirty years ago, when we were still a traditional steel group, we completely reinvented ourselves, taking the courageous decision to dismantle our blast furnace and invest in an electric arc furnace. This has already enabled us to avoid large quantities of greenhouse gases over the last few decades. We work to fulfill the Paris Climate Agreement –the global community’s commitment to reduce global warming. Green steel is crucial for a sustainable future – in industries worldwide. And green steel is what we produce.
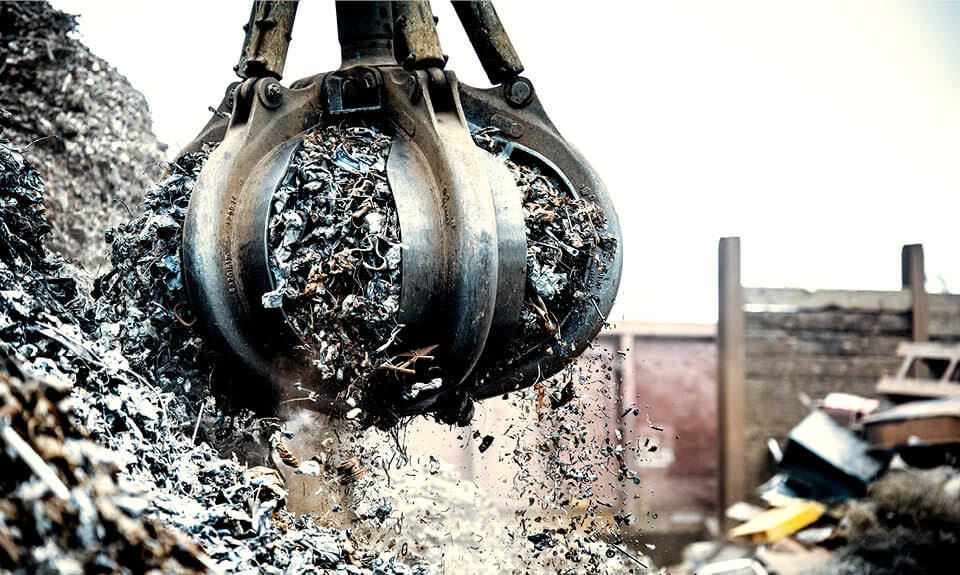
Turning scrap into
high-tech steel
We are enabling a circular economy. By melting steel in our electric arc furnaces from almost 100 percent scrap metal, we transform waste material into high-tech products – without any loss of quality. Not only do our sources of scrap metal include products that have completed their life cycles, but we can also feed production scrap, for example from our customers, directly back into the steel production process. The infinite recyclability of steel means that every recycling process improves our product’s carbon footprint. We also recycle slag, a byproduct which can be used in road construction, for example. This is how we produce green steel in a closed loop that effectively reduces greenhouse gas emissions.
Become a
decarbonization pioneer with us
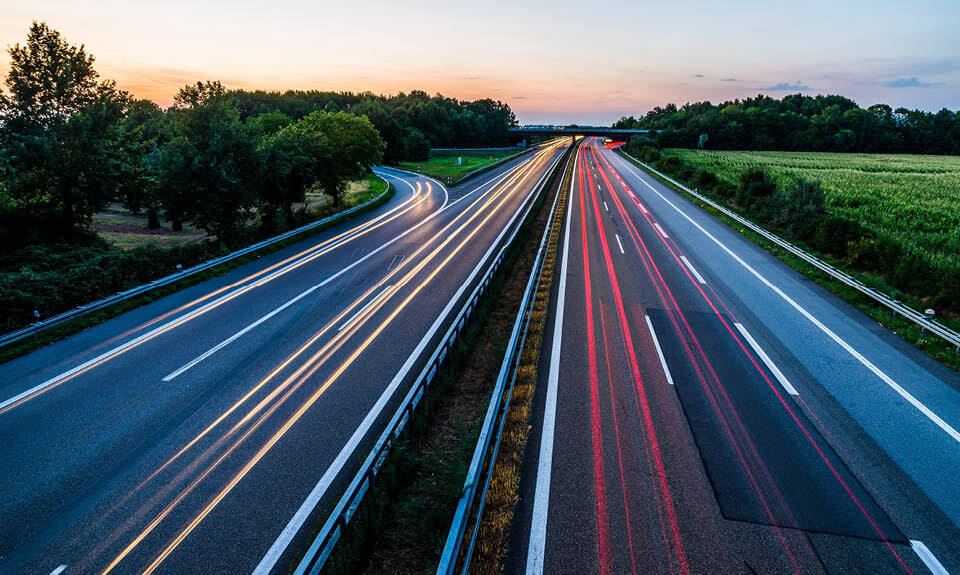
We are making a difference to industries around the world with our green steel. Are you looking for sustainable solutions for your market?
Green Steel product lines
Three product lines, one goal:
to cut CO2 emissions
Under the Green Steel label, we offer three product lines that all significantly reduce CO2 emissions during steel production compared with traditional blast furnaces.
The green steel in all three product lines is produced in our electric furnace from almost 100 percent scrap metal.
Our Green Power Steel is made using 100 percent renewable electricity.
Green Power Premium Steel also uses 100 percent biogenic carbon.
Scope 1: direct emissions from plant / production process
Scope 2: indirect emissions from purchased electricity
*CO2 emissions relate to crude steel produced (continuously cast)
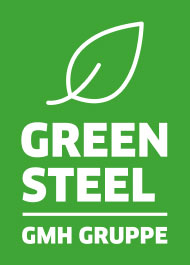
Under the Green Steel label, we offer three product lines that all significantly reduce CO2 emissions during steel production compared with traditional blast furnaces.
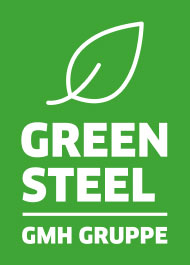
How much steel do you need per year?
CO2-emissions saved*
(Scopes 1+2)
8.624 metric tons
Crude steel compared with traditional blast furnace
Money saved in carbon credits
€301.840
GMH Gruppe premise: 100€/metric ton
Want to save even more? Switch between our three product lines.
Green Steel
Process
Electric furnace
Green Steel
Green Power Steel
Process
Electric furnace
Energy source
100%
renewable electricity
Green Steel
Green Power Premium Steel
Process
Electric furnace
Energy source
100%
renewable electricity
Fuel
100%
biogenic carbon
Carbon footprint
High-precision carbon footprint calculations for many product variant
Not only are we pioneers in the production of green steel – we also set standards in the calculation of carbon footprints. At Georgsmarienhütte GmbH, we calculate the carbon footprints of over one million product variants with extremely high levels of accuracy and reliability – in a process certified by TÜV SÜD. You can use this data to analyze decarbonization along your supply chain, provide precise figures to support your legally prescribed and self-imposed climate targets – and lead your company into a sustainable future.
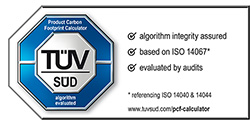
Our roadmap for the future
Zero CO2 emissions
by 2039
We take our responsibility for sustainable steel production seriously. Based on decades of experience and our expert knowledge base, we are constantly improving our technology. Our goal is clear and ambitious: We want to reduce our CO2 emissions to zero by 2039 (Scope 1+2). As an interim step, we will halve our current CO2 emissions yet again by 2030.
Our measures for CO2 reduction
Green electricity. Green carbon. Green hydrogen.
Our strategy for climate-neutral steel production is based on three key measures
The following information relates to Scopes 1 + 2
Scope 1: direct emissions from plant / production process
Scope 2: indirect emissions from purchased electricity
Product carbon footprint (PCF) relates to volume of crude steel produced (continuously cast)
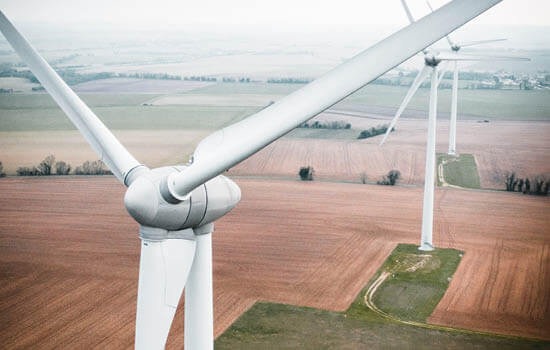
Electricity from renewable sources instead of fossil fuels
We install photovoltaic systems at our sites and invest in local photovoltaic systems. In the future, we intend to invest in partnerships with wind farms. In addition, we purchase green electricity from certified sources.
Reduction of CO2 emissions
from 0.4 to 0.1 metric tons
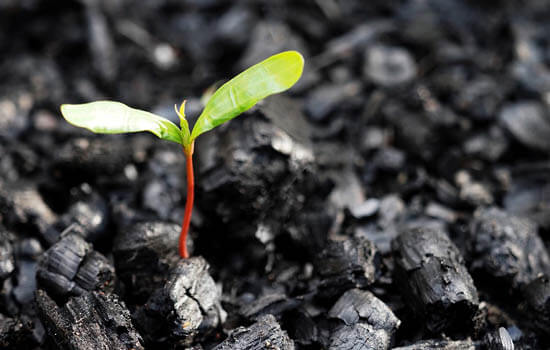
Green carbon
instead of fossil coal
We are implementing a wide range of efficiency measures to reduce our coal consumption. We are gradually replacing coal with biogenic carbon. Our goal is to produce 50 percent of our steel using 100 percent biogenic carbon as early as 2030.
Reduction of CO2 emissions
from 0.4 to 0.05 metric tons
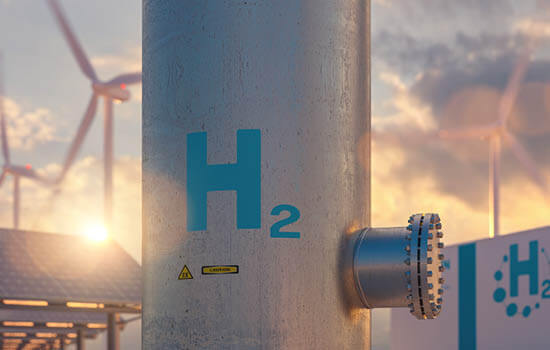
Green hydrogen
instead of natural gas
We are implementing a wide range of efficiency measures to reduce our gas consumption, and are gradually transitioning to hydrogen in our production processes. We are also looking into the possibility of producing green hydrogen ourselves. To ensure the future supply of hydrogen to our plants, we are closely involved in technical and political discussions concerning the design of Germany’s hydrogen infrastructure.
Reduction of CO2 emissions
from 0.4 to 0 metric tons
Would you like to join us as a decarbonization pioneer?
With us, you can lead your company into a green future.
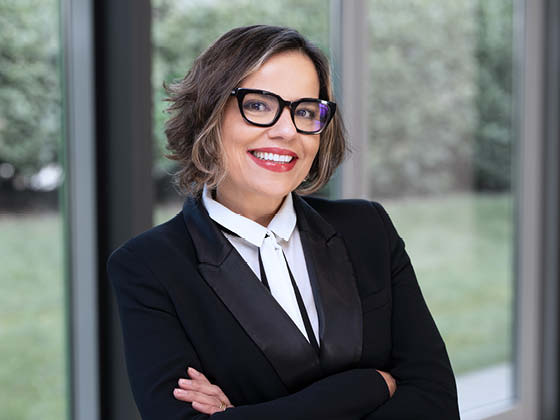
Luciana Filizzola
Director Sustainability and Communications