Turning scrap into excellence,
into climate action
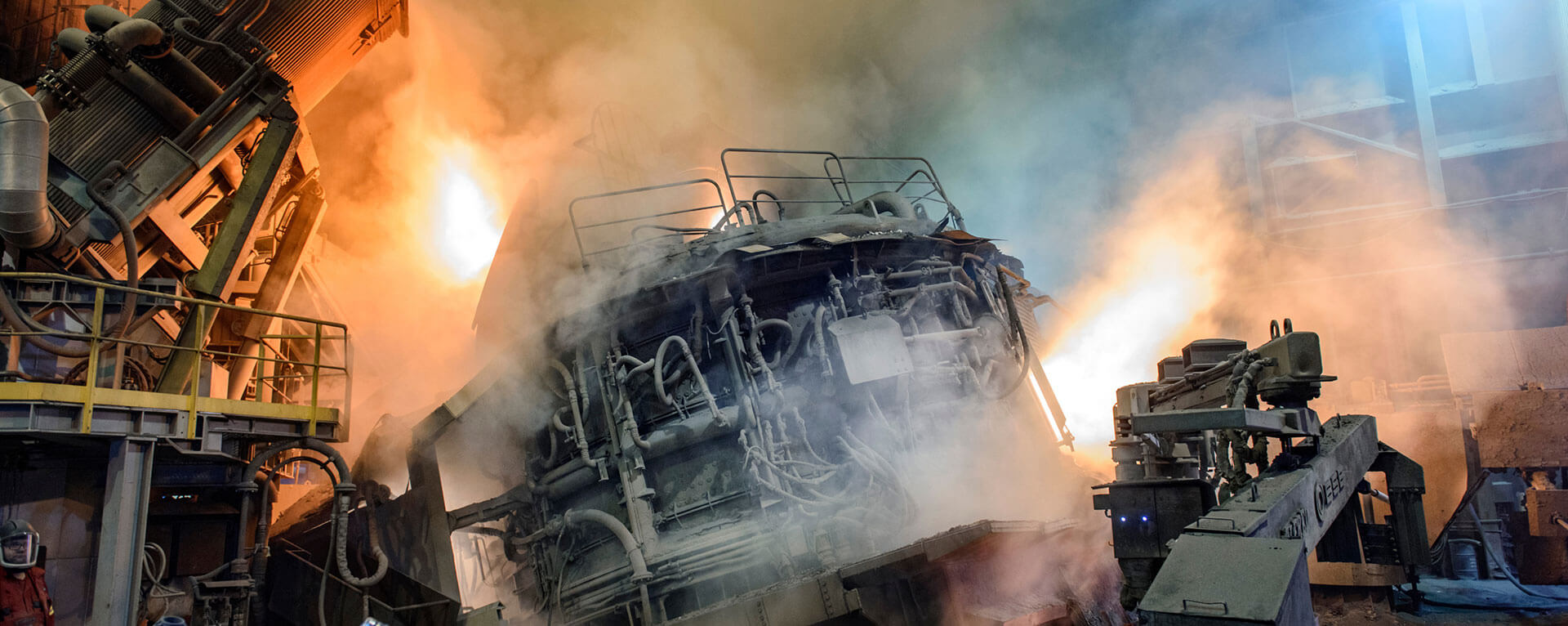
From crude steel to ready-to-install components: steel products that add sustainable value
We are shaping the future of steel by placing sustainability at the heart of our manufacturing processes. Our closed-loop system produces green steel that benefits our customers and our planet.
Recycling scrap
Scrap as the foundation of our steel value chain
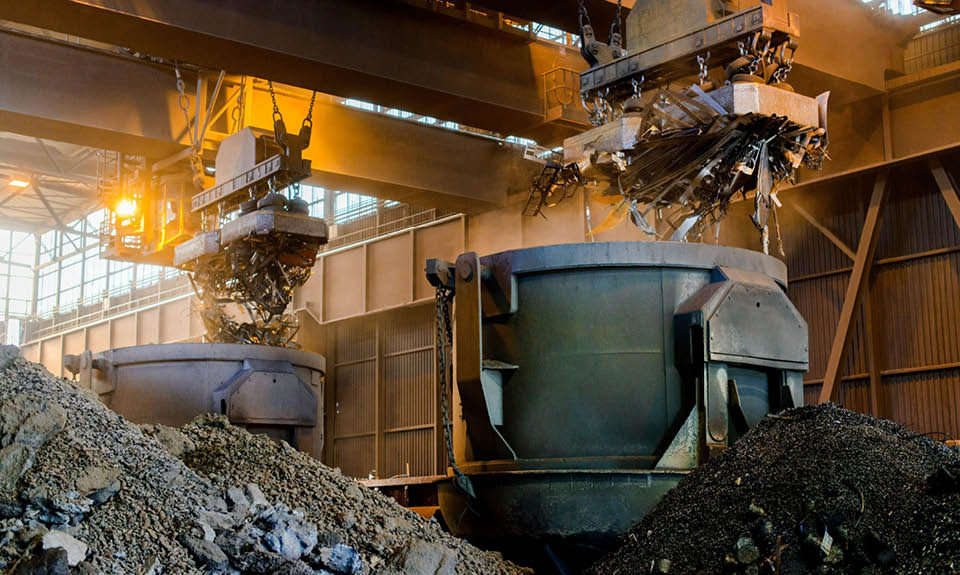
Scrap is the basis of our steel production: our high-tech products are made from almost 100 percent scrap metal. In this way, we avoid mining new raw materials and conserve our natural resources. We process steel scrap, special scrap and non-ferrous metal scrap so that it can be reused. We also make use of recirculated scrap such as offcuts and shavings in our steel production process.
Steel scrap
We reuse unalloyed steel scrap directly in our steelmaking plants as a raw material for new products.
Special scrap
We break down ferrous byproducts from pig iron and steel production into weights and sizes suitable for use in a furnace.
Foundry scrap
We supply foundries with processed recycled raw materials tailored to their requirements.
Alloyed steel scrap
In addition to its iron content, alloyed steel scrap contains components that make the steel more resistant to heat and corrosion.
NF metal scrap
Our portfolio also includes NF scrap, i.e. all scrap made from non-ferrous metals.
Grinding sludge
We process grinding sludge in our briquetting plant ready for material recycling in steelworks.
The electric arc furnace
Our climate champion
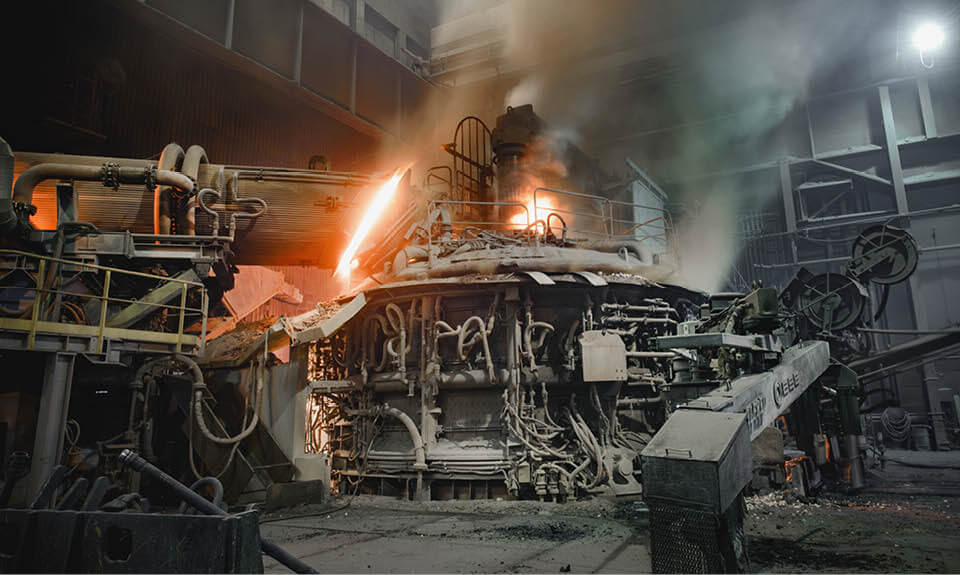
We produce steel from recycled scrap in the most sustainable way possible: in an electric arc furnace. Compared with traditional blast furnaces, it emits less CO2, consumes less energy and minimizes harmful air pollutants. In addition, the electric furnace can be flexibly controlled based on demand, without being tied to continuous operating cycles like integrated steelworks. Increasingly, we rely on renewable energy sources to operate our furnace, thereby continuously improving our carbon footprint.
1 Melting:
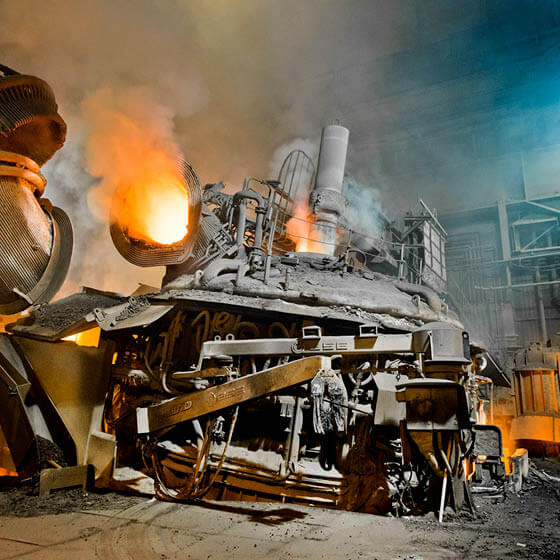
The scrap is melted down in the electric arc furnace. The electric arc between the graphite electrodes reaches temperatures of up to 3,500 degrees Celsius.
2 Tapping:
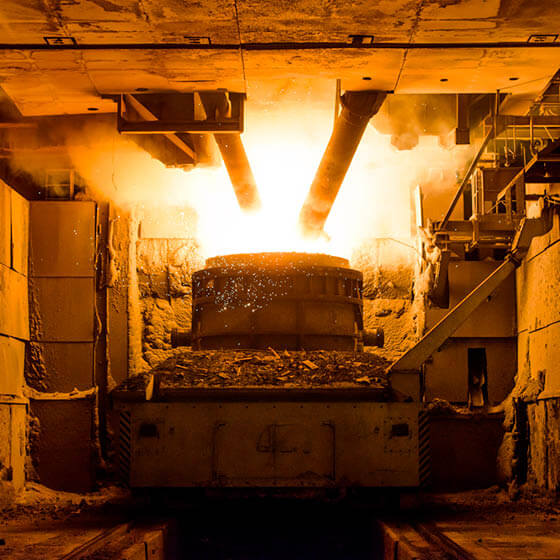
The molten steel runs into the ladle through a refractory tube in the furnace floor. The addition of alloying elements gives the steel exactly the right properties for the customer’s end product.
3 Continuous casting process:
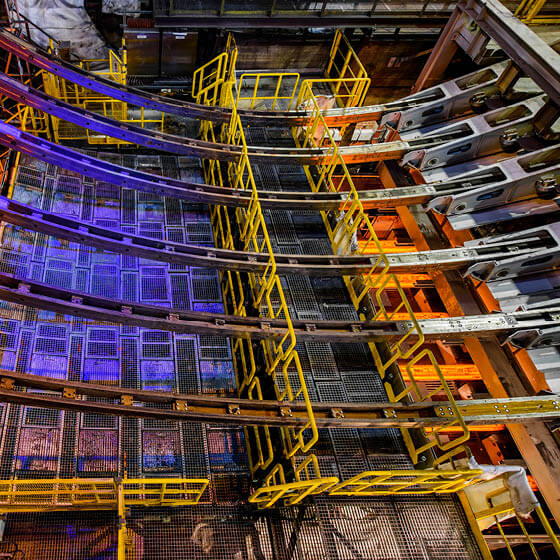
The molten steel is then cast without interruption.
4 Flame cutting machine:
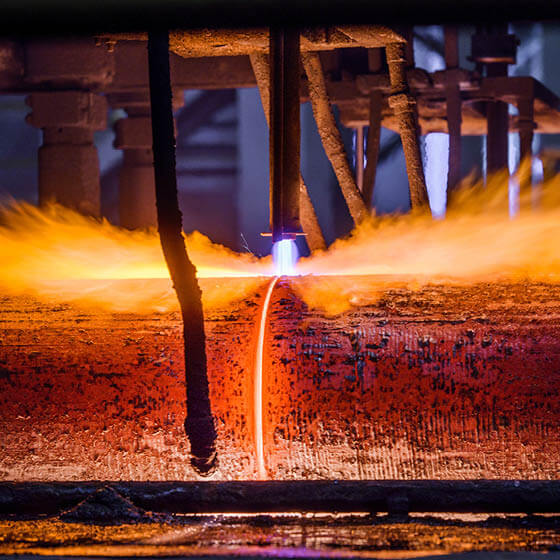
Depending on the customer’s specifications, the steel is cut using either continuous or ingot casting, cooled in the turning bed and checked for quality in the finishing area. After this, it is ready to be dispatched.
How we use our electric furnaces
to produce Green Steel
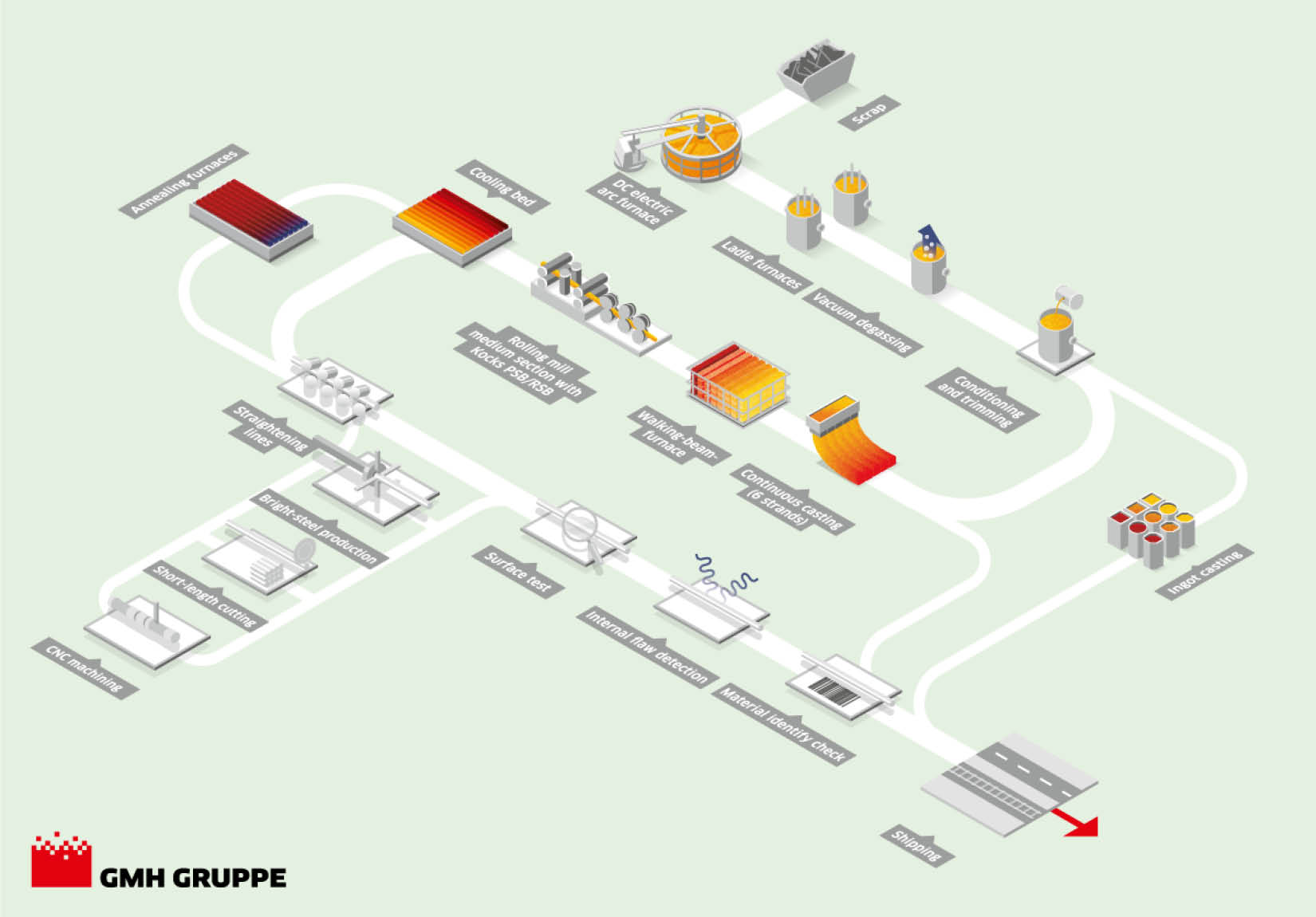
Green Steel products
From crude steel to
high-tech steel
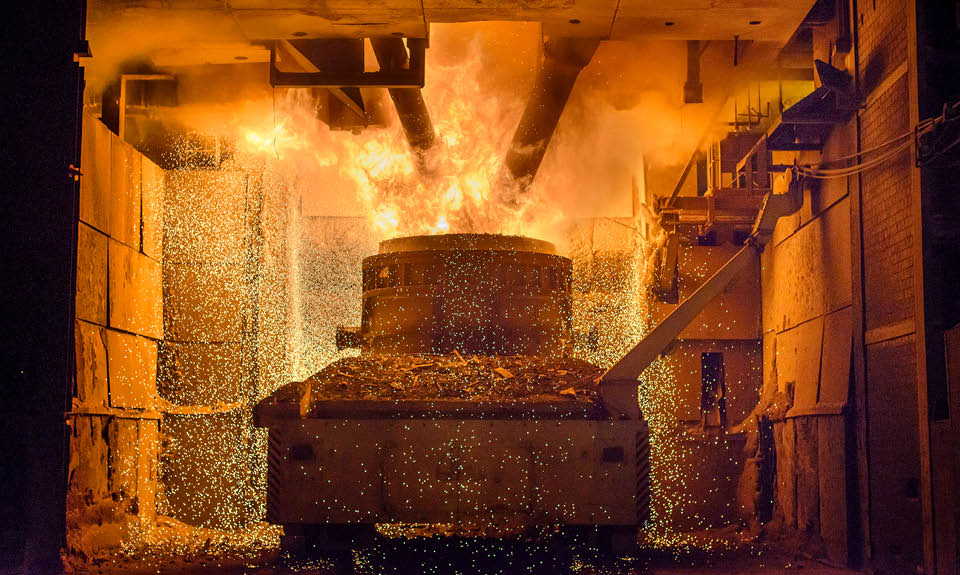
We supply steel products that have been processed to various levels – as several sustainable Green Steel variants that all meet the highest quality standards.
Closed-loop manufacturing
Maximum sustainable
value creation
Our aim is to productively reuse resources and materials over and over again, to take full advantage of synergies along the entire value chain. This is why we rely on integrated product and energy cycles in our value stream, which we are constantly improving.
Our path to CO2-neutral steel production
We have made a promise to ourselves and future generations: By 2039, our steel production activities will no longer produce any CO2 emissions (Scope 1+2).
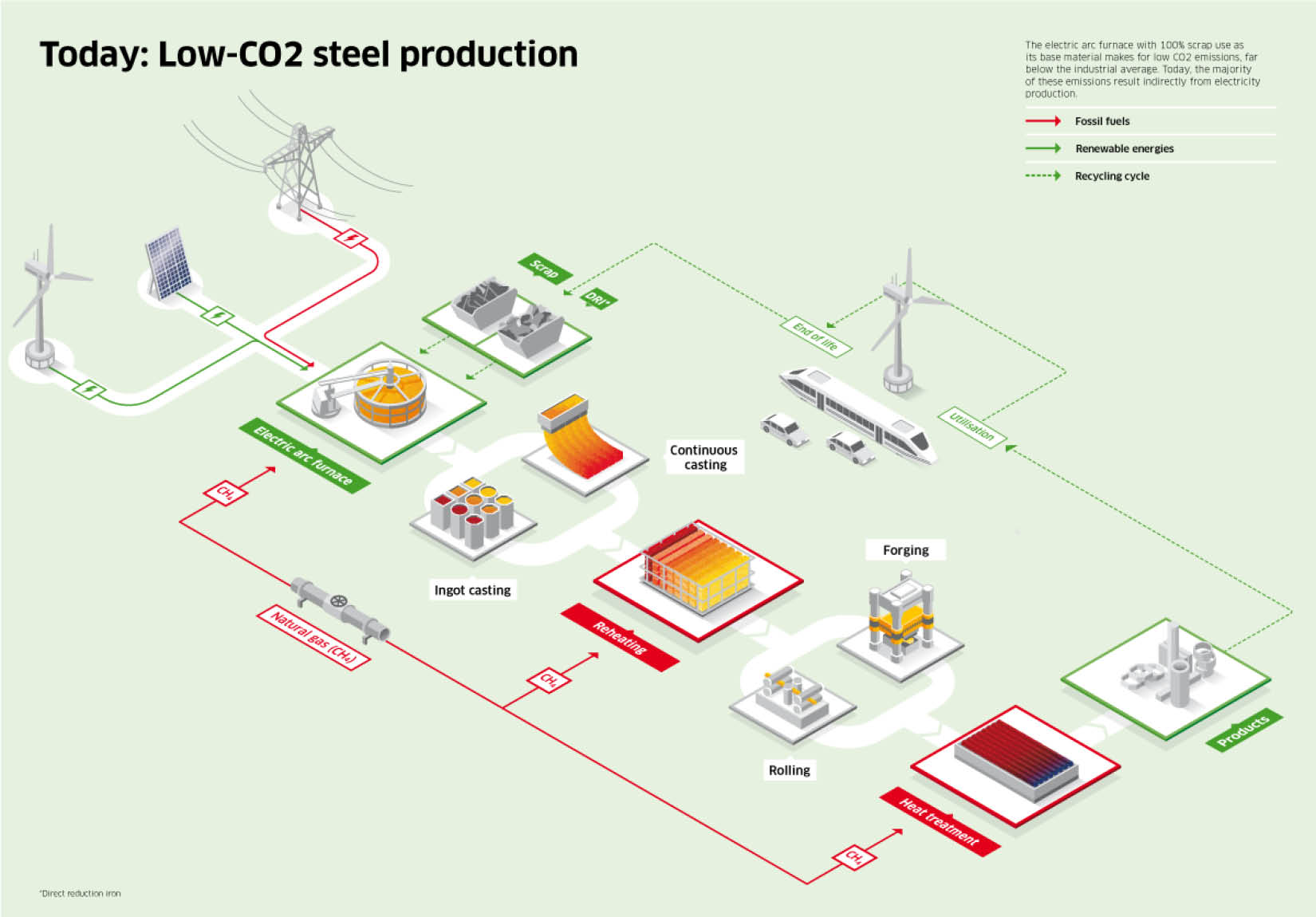
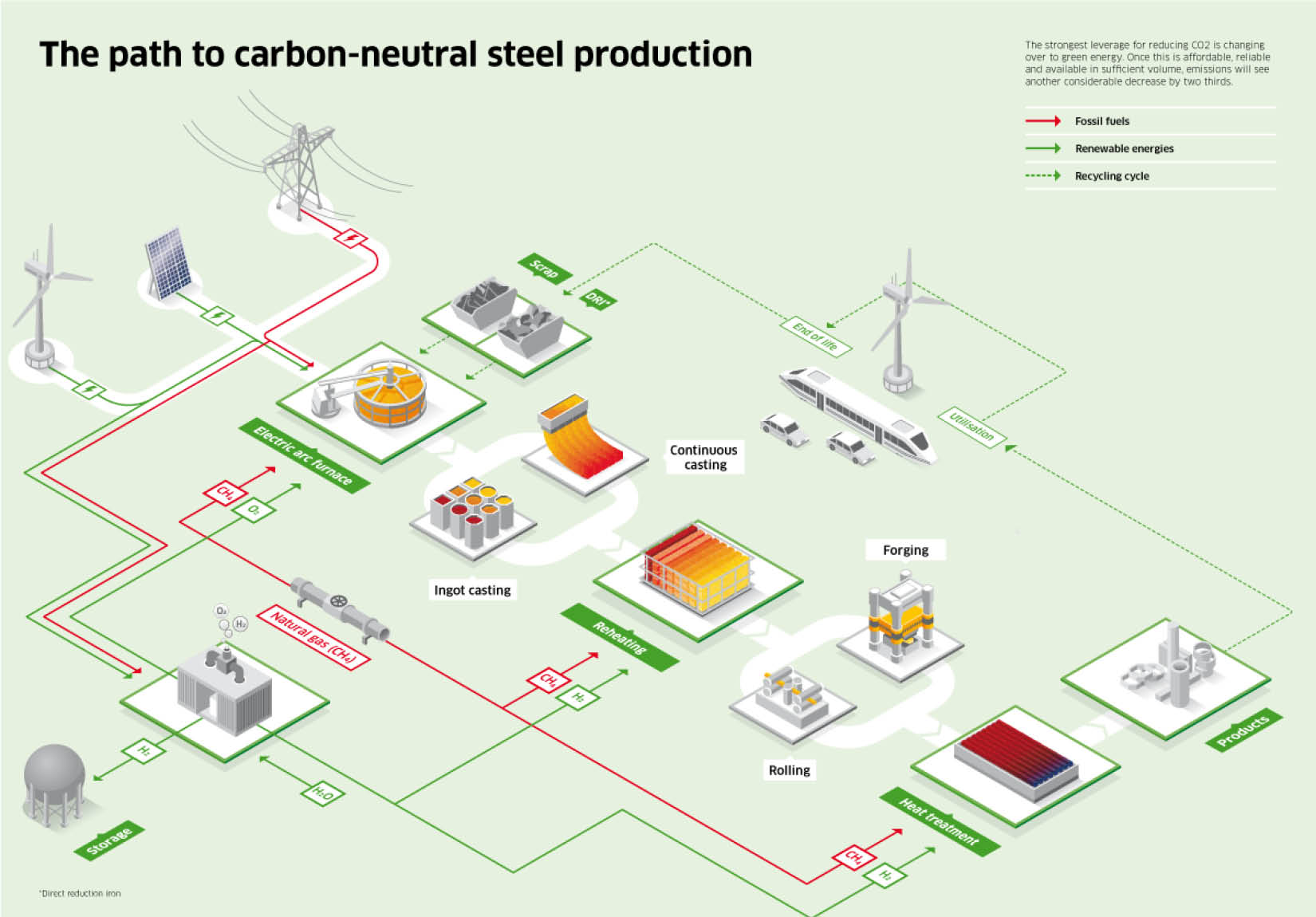
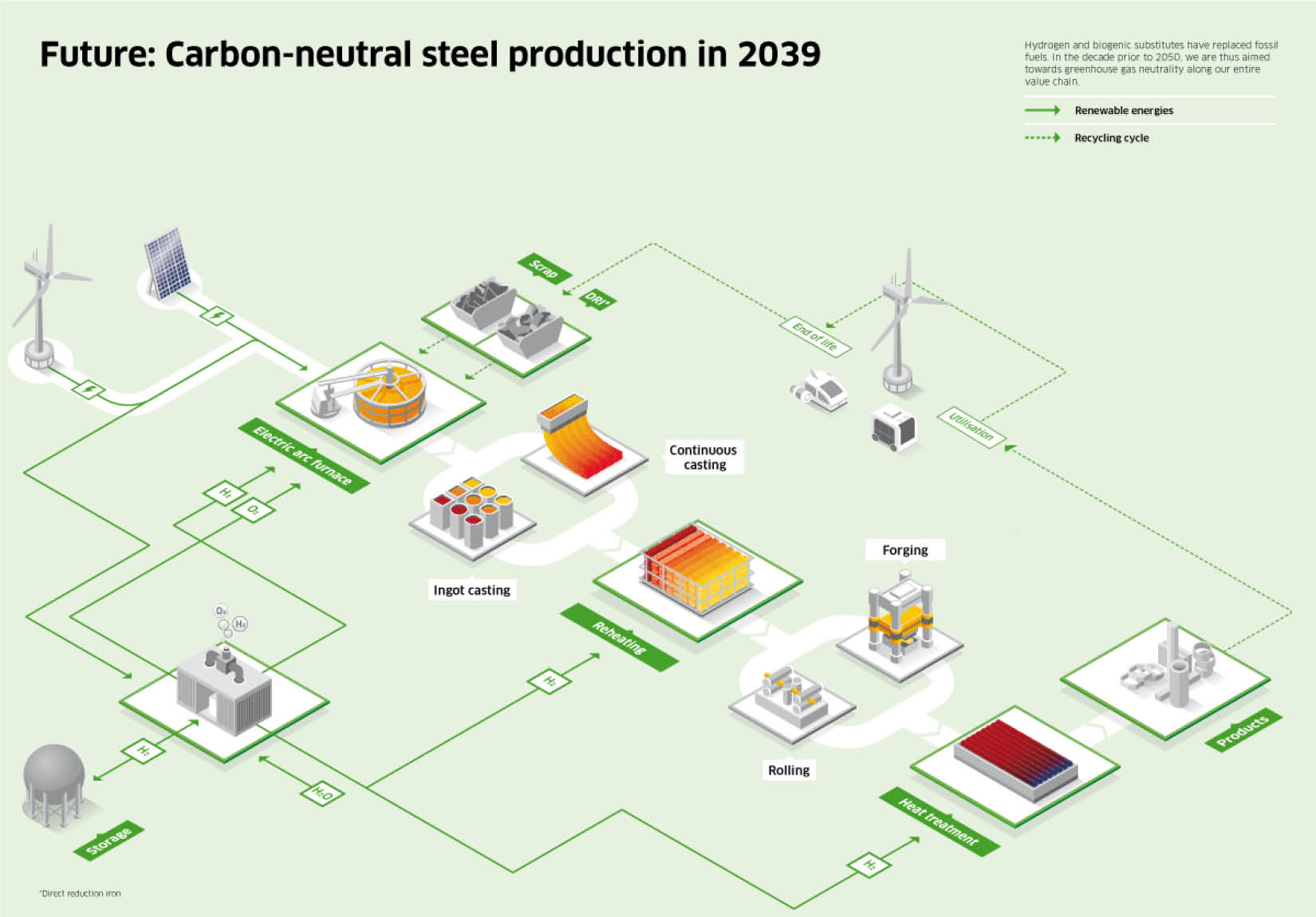
Would you like to join us as a decarbonization pioneer?
With us, you can lead your company into a green future.
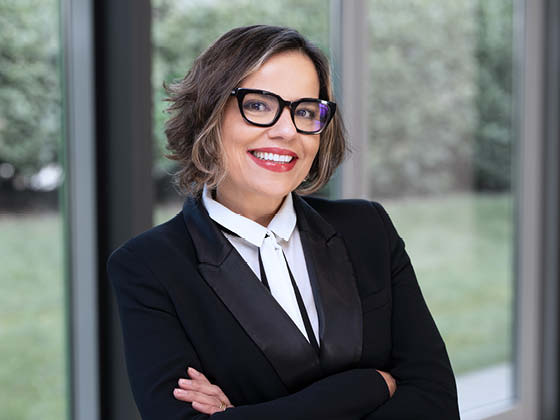
Luciana Filizzola
Director Sustainability and Communications