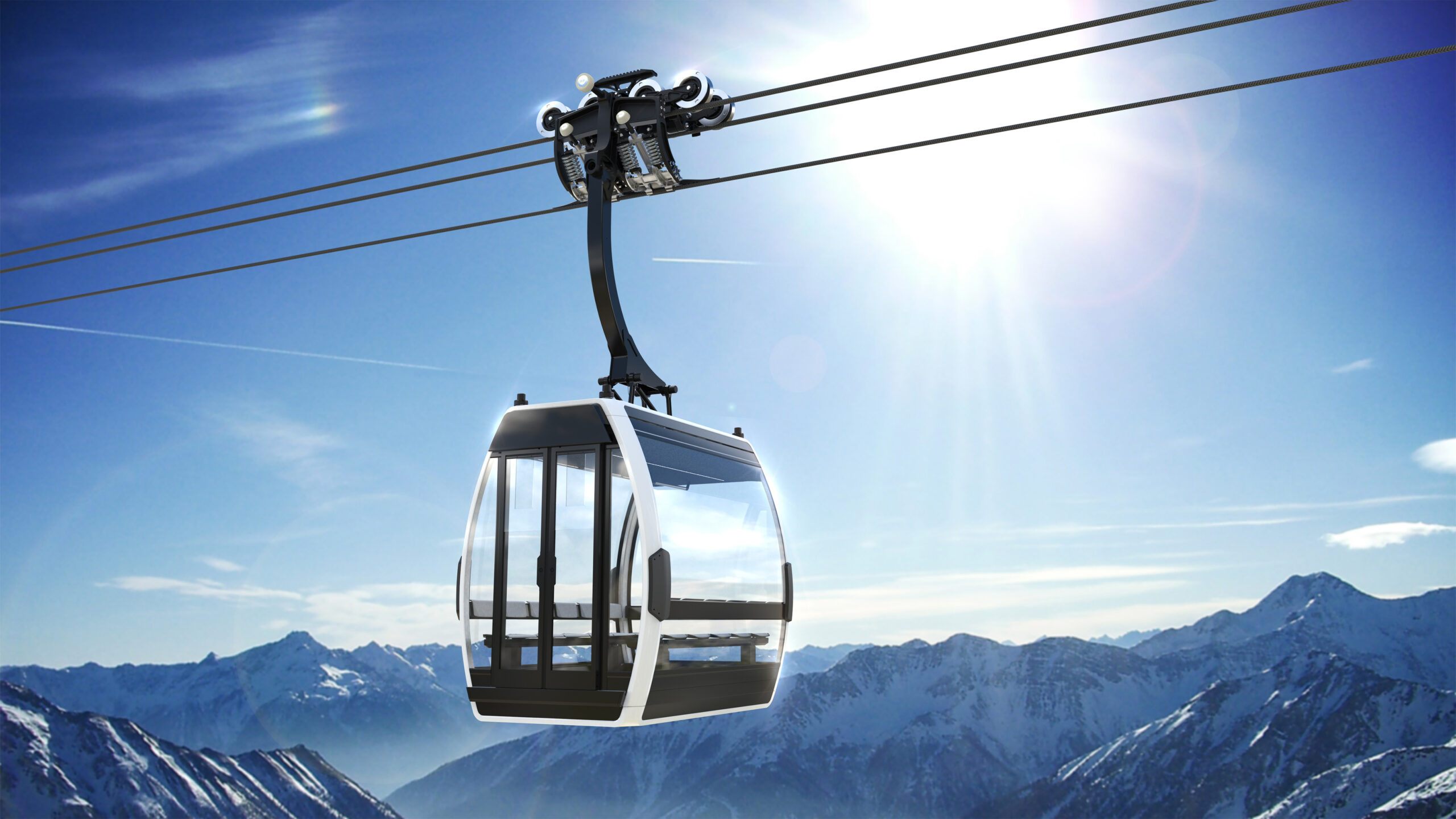
GMH Gruppe supplies key components for the TRI-Line
Innovative technology for the future of passenger transport
In Hoch-Ybrig, Switzerland, the new TRI-Line ropeway from Doppelmayr is replacing a 55-year-old reversible aerial tramway. The TRI-Line is compact, wind-stable and can transport up to 8,000 people per hour. GMH Gruppe (GMH) supplied three essential components for this project, which are not only crucial in terms of safety and stability but also had to fulfil the high requirements for lightweight construction and precision.
Challenge: Complex geometries in lightweight construction
Manufacturing the components for the TRI-Line presented an extraordinary challenge. The project demanded highly complex geometries to save weight without compromising stability. In particular, the clamp lever, the rocker support and the main clamp part had to be manufactured in such a way that they could absorb the enormous forces that act in ropeway technology and at the same time be precisely integrated into the design. For example, the main clamp part, a key component weighing 70 kilograms, carries the springs that hold the vehicle on the cable – a task that requires maximum precision and strength.
Solution from GMH: New production technologies and close collaboration
In order to fulfil these requirements, GMH relied on state-of-the-art forging technologies. The new stretching machine, which performs crucial preparatory work during the forming process, was a key factor in this. It made it possible to prepare the components with their complex geometries precisely and efficiently. Several forming simulations and close technical dialogue with Doppelmayr were necessary to produce the components in accordance with the drawings. Finally, the components underwent numerous tests, including ultrasonic and crack tests, to ensure the highest quality and safety.
Lightweight construction and sustainability in the Alps
The TRI-Line not only offers more comfort with new cabins but is also environmentally friendly in its construction. The lightweight construction reduces the cable car’s ecological footprint and the compact design blends harmoniously into the landscape. Thanks to its robust and lightweight construction, the TRI-Line can easily cope with the challenging wind conditions in Hoch-Ybrig.
A total of 35 tonnes of steel were used to manufacture around 300 parts for the cable car project – a milestone in the collaboration between GMH and Doppelmayr and further proof of GMH Group’s innovative strength in modern lightweight construction technology.
Photo © Doppelmayr
Would you like to join us as
a decarbonization pioneer?
With us, you can lead your company into a green future.