Used as a pre-material for transmission and engine components
Automotive industry
Sustainable solutions
for personal mobility – now and in the future
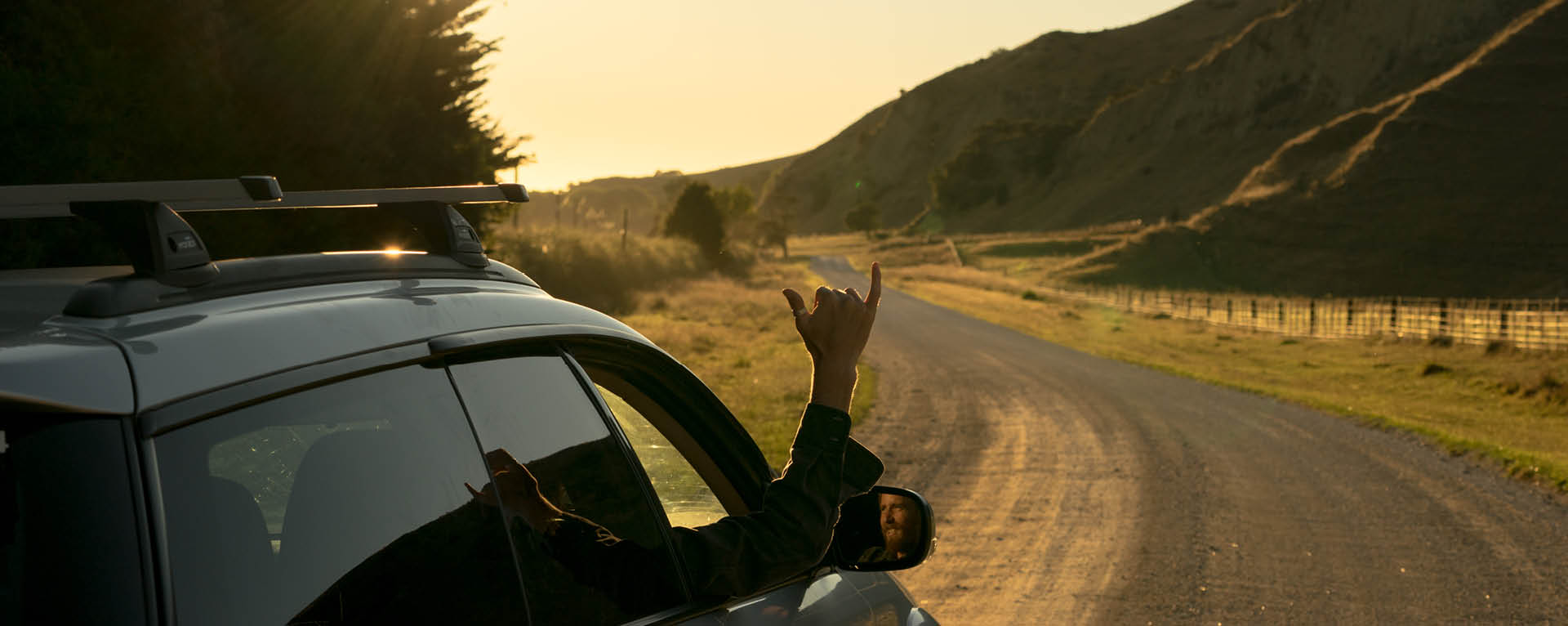
Together with our customers, we develop pioneering solutions for the automotive industry: from initial idea to primary material right through to ready-to-install components
Our steel is produced in electric arc furnaces. Rolled, forged and – if required – further processed by machine, it forms the basis for safety-critical mobility applications. Our production processes and lightweight construction concepts help to reduce emissions and fuel consumption while meeting the highest quality standards. As an essential partner to the automotive industry, we supply solutions for both conventional and electric vehicles – from rolled steel bars as a primary material for the production of transmission and engine components such as connecting rods or rotor shafts, through to ready-to-install steering racks.
4 out of 5
Vehicles made in Germany contain steel from GMH Gruppe.
Market trend: drivetrain electrification
Electric motors
Demand for electric cars continues to rise worldwide. Studies assume that around half of all vehicles sold in 2030 will be electric. The motors of these vehicles require highly resilient steel components. These include, for example, rotor shafts for electric motors, which are made from our steel.
Green Steel for the automotive market
Low emissions
for a greener future
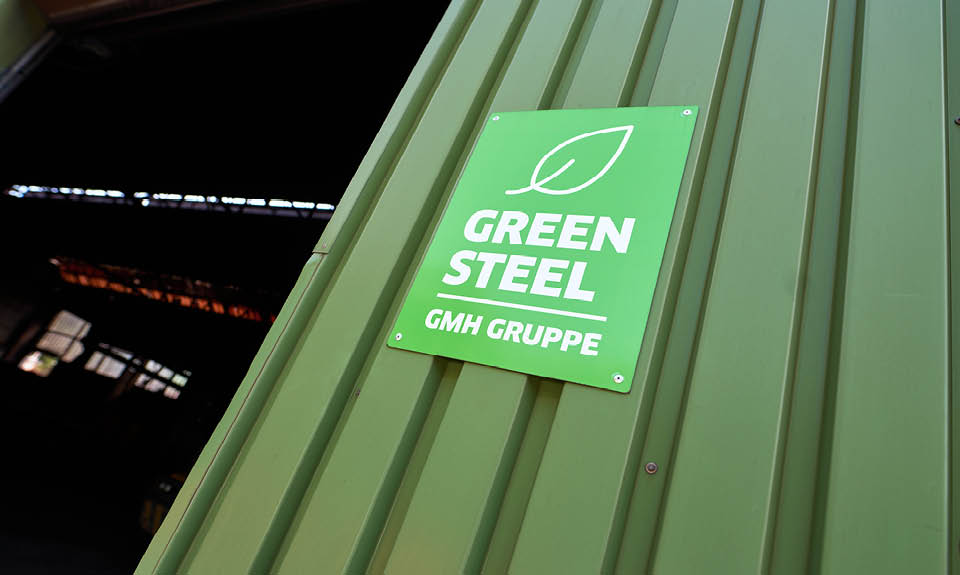
Reducing CO2 emissions is vitally important to the automotive industry. Among other things, manufacturers are focusing on more environmentally friendly production technologies, recycling raw materials and improving the life cycle impacts of their vehicles. This includes the production and sale of electric and hybrid vehicles. Together with car manufacturers and their suppliers, we are developing low-emission, recyclable steel products for various mobility applications – green steel for green mobility.
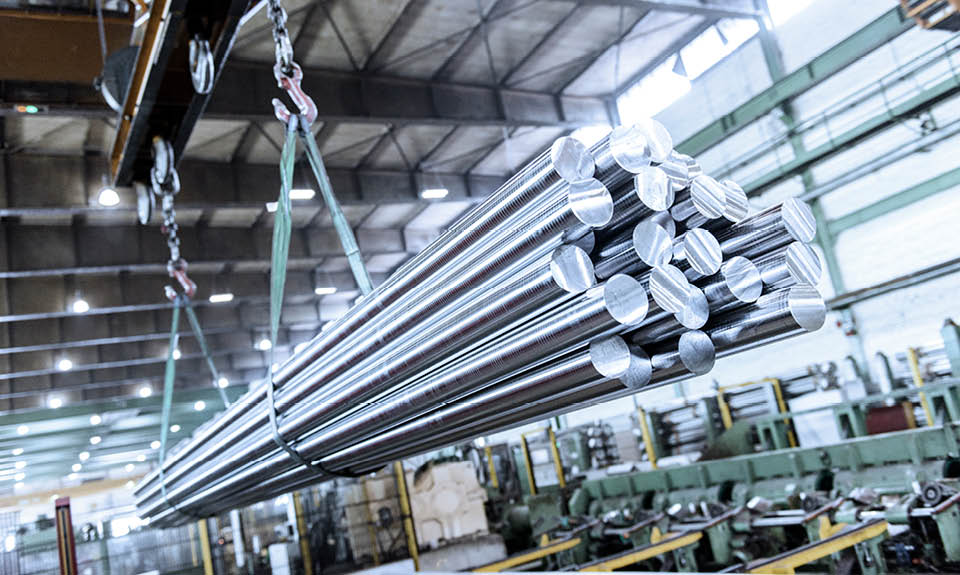
High-precision carbon footprint calculations for 1,000,000 product variants
We calculate the carbon footprints of over one million product variants with extremely high levels of accuracy and reliability – in a process certified by TÜV SÜD. As an automotive manufacturer or supplier, you can use this data to analyze decarbonization along your supply chain and provide precise figures to support your legally prescribed and self-imposed climate targets.
What you can expect
Lightweight materials that save fuel
Lightweight construction is becoming increasingly relevant, especially for drivetrain and chassis components in passenger cars and commercial vehicles. For this reason, our materials development department, working with other specialists in the Lightweight Forging Initiative, has developed almost 2,000 ideas – for our innovative 46MnVS5 material, for example. This high-strength steel makes crack connecting rods ten percent lighter.
High-strength steels to increase safety
Working closely with our customers, we have developed two new types of steel that can be produced with significantly less energy than before: bainitic forged 16MnCrV7-7 steel, and 50CrMnB5-3 steel, which is induction-hardened following semi-hot forming.
Low-emission electric steel that reduces CO2
Alongside the goal of reducing CO2 emissions from transportation, it is becoming increasingly important to manufacture the vehicles themselves in a low-emission process. The steel from our electric furnaces already causes 80 percent fewer CO2 emissions than conventional steel production.
In use
From product to application
Our high-quality steel products are used in many automotive applications. Here are a few examples.
Steel bars (rolled)
Steering component
In use as a steering component for passenger cars
Special profiles
Used as a connecting element between car door and vehicle
Bright steel
Used for gear shafts and the bottom brackets of e-bikes
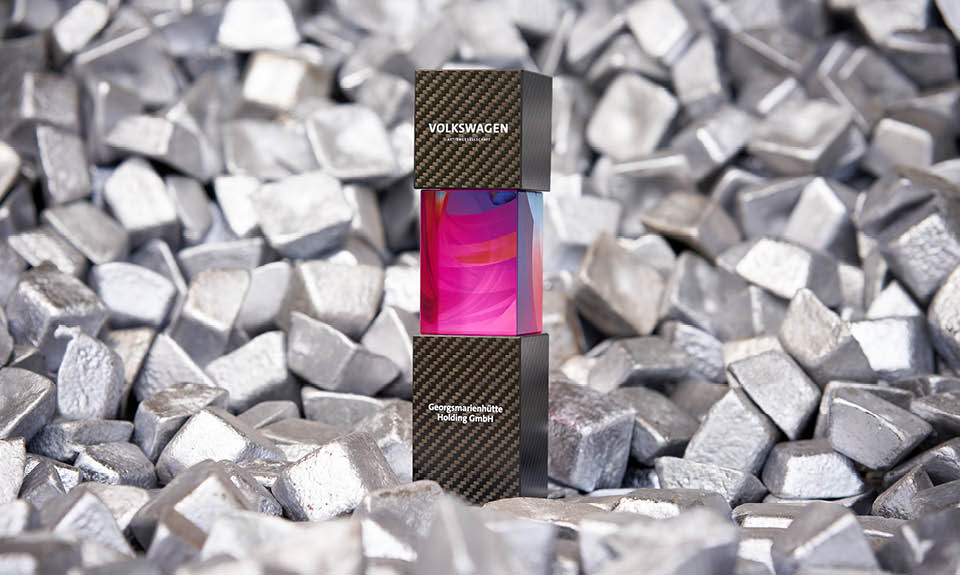
Award-winning
Most sustainable supplier to the Volkswagen Group
Volkswagen Osnabrück supplies our Georgsmarienhütte steelworks with scrap metal generated during the production process. There, the scrap is recycled into new high-tech steel bars. These in turn are delivered to the Volkswagen plant in Baunatal for the production of transmission components, ensuring that 100 percent of recyclable materials find their way back into the loop.
Would you like to join us as
a decarbonization pioneer?
With us, you can lead your company into a green future.