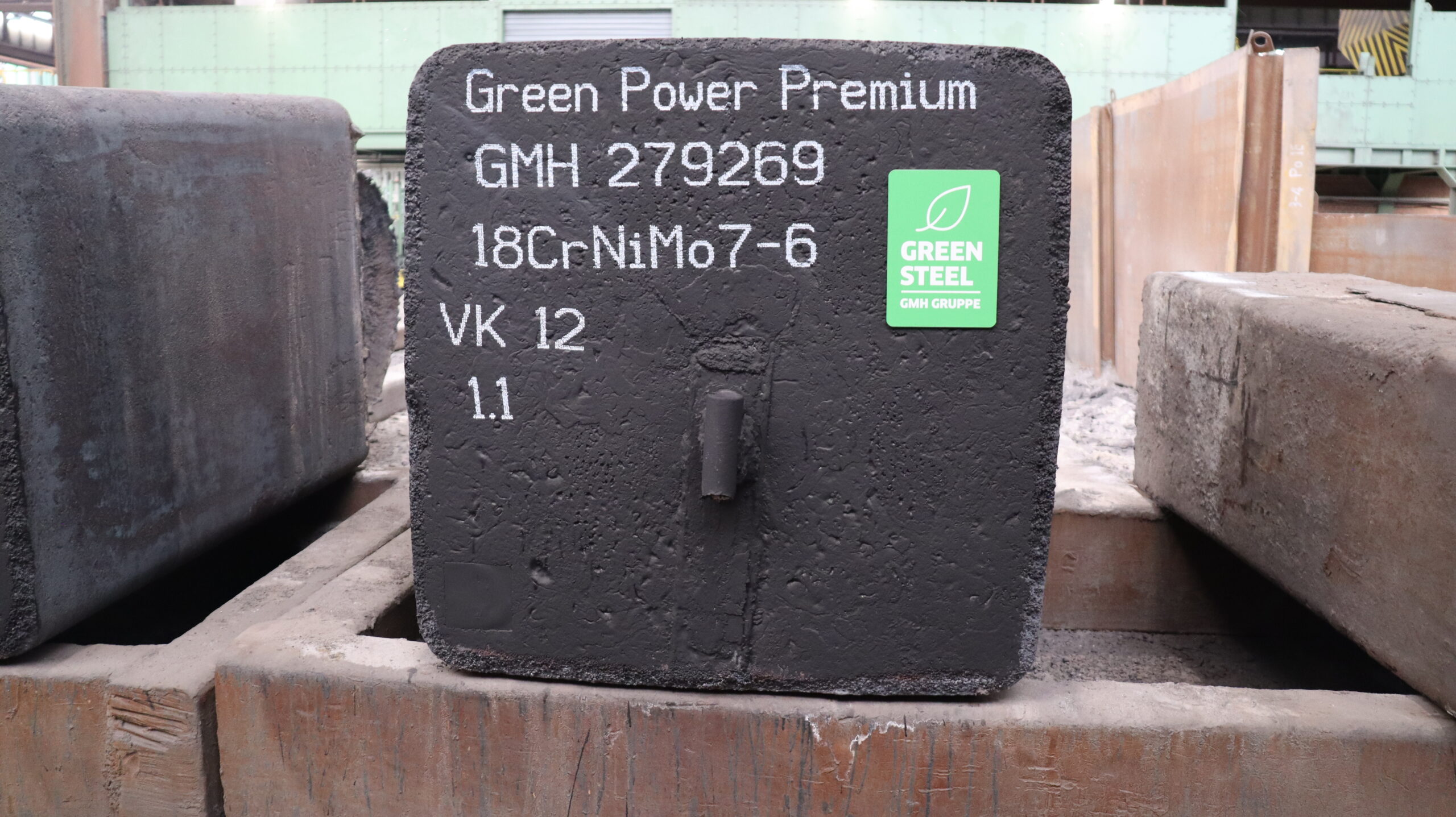
Georgsmarienhütte, 10 April 2025
From Tradition to Transformation: Hammerwerk Erft commits to Green Power Premium Steel from GMH Gruppe
The long-established company uses 98 per cent CO₂-reduced steel from Georgsmarienhütte for sustainable forged products in a strategic partnership with GMH Gruppe
Hammerwerk Erft G. Diederichs GmbH & Co. KG is now using Green Power Premium Steel from Georgsmarienhütte GmbH – an important step towards climate-neutral forging. The first delivery of 120 tonnes of Green Power Premium Steel to the long-established company, based in Bad Münstereifel, marks the beginning of a closer partnership between the traditional forging specialist and Georgsmarienhütte GmbH, a GMH Group company.
The steel, manufactured using 100 per cent renewable energy from biogenic coal, offers a reduction in CO₂ emissions of up to 98 per cent and is therefore currently the lowest-emission steel available in Germany.
Georgsmarienhütte GmbH has been a pioneer in the field of sustainable steel production in Germany for over three decades. At the core of its production process is the direct-current electric arc furnace, that relies almost entirely on scrap metal. This production method alone is responsible for around 80 per cent lower CO₂ emissions than occur with the classic blast furnace method.
Green Power Premium Steel – Steel with a particularly low CO₂ footprint
With its product ‘Green Power Premium Steel` Georgsmarienhütte GmbH goes further than the requirements of classic low-emission electric steel production: The steel is melted with 100 per cent renewable electricity and the sole use of biogenic coal ensures a climate-friendly alternative to fossil coal. This so-called biochar is produced by the pyrolytic carbonisation of certified wood waste. The result: a 98 per cent smaller carbon footprint (scope 1+2) compared to steel produced in a conventional blast furnace.
Certified sustainability – transparent and verifiable
Green Power Premium steel products are certified by guarantees of origin for the green electricity used in their production. The Product Carbon Footprint (PCF) is calculated according to a method validated by Germany’s technical inspection body (TÜV Süd). It includes the requirements of the ISO 14067 and 14044 standards and the specifications relating to the Greenhouse Gas Protocol covering the calculation of greenhouse gas emissions and the associated reporting required from companies. The CO₂ emissions are recorded transparently along the entire value chain, from ‘cradle to gate’. Georgsmarienhütte GmbH can provide a precise, product-specific PCF calculation for over 1,000 steel variants.
Strong partnership with a focus on climate neutrality
Hammerwerk Erft G. Diederichs GmbH & Co. KG has been a long-standing customer for ingots and continuously cast blooms from Georgsmarienhütte GmbH, and a strategic partner of the GMH Group. The tradition-rich family company specialises in high-quality forged items as an open-die forger and a producer of seamless rolled rings.
Marc Schmitz, Managing Director of Hammerwerk Erft, explains: “As a family-owned company, with a long tradition in the forging industry, we know how crucial sustainable solutions are for the future – especially in an industry like ours. With the first ingot melt from Green Power Premium Steel, we are taking an important step towards climate-friendly production, together with Georgsmarienhütte. We are pleased to be taking this path with a strong partner at our side.”’
Frank Agel, Managing Director of Georgsmarienhütte GmbH, adds: “With our high-quality product ‘Green Power Premium’ we can actively support the decarbonisation of our customers’ applications. We are delighted to be able to support our long-standing business partner Hammerwerk Erft in this endeavour with the first batch of ‘Green Power Premium Steel’ for their products.”
With this successful delivery, both partners are sending a clear signal in support of a more climate-friendly steel and forging industry.
About GMH Gruppe
GMH Gruppe is a full-range supplier of steel as a primary material from melted scrap through to ready-to-assemble components. It is one of the largest privately owned metal processing companies in Europe. The group includes 20 medium-sized production companies in the steel, forging and casting industries, which are represented in over 50 countries. With more than 6,000 employees, GMH Gruppe generates an annual turnover of about 2,3 billion euros.
GMH Gruppe is a pioneer in sustainable steel production and has been accepted into the ‘Association of Climate Protection Companies’. Based on the recycling of scrap metal, the company produces green steel and thus makes an important contribution to the circular economy. The use of electric arc furnaces at four sites reduces CO2 emissions by a factor of five compared to conventional blast furnaces. This also reduces the CO2 footprint of the customers supplied by GMH. These include companies worldwide from the automotive industry, mechanical and plant engineering, railway technology, power generation, transport logistics, aerospace, agriculture and construction machinery sectors. GMH Gruppe has set itself the goal of being completely climate-neutral by 2039. Further information can be found at www.gmh-gruppe.de/en/
About Georgsmarienhütte GmbH
Georgsmarienhütte GmbH from Georgsmarienhütte in Lower Saxony is one of Europe’s leading suppliers of crude steel, bar steel and bright steel made from quality and engineering steels. The company also manufactures pre-processed and, in some cases, ready-to-install components. Georgsmarienhütte is already one of the most climate-friendly steel companies in Germany. With its comparatively low CO₂ value chain, in which scrap is melted in the electric arc furnace and recycled into new steel, it makes an important contribution to the circular economy and is a pioneer in sustainable steel production. The methodology used by Georgsmarienhütte to calculate the product carbon footprint (PCF) has been validated by TÜV SÜD and is now used for more than a thousand steel variants.
In addition to the automotive industry and its suppliers, customers are served in particular in mechanical and plant engineering and the energy industry. Steel from Georgsmarienhütte is used wherever the load is greatest, where power is generated or transmitted and safe and wear-resistant operation is important.
For inquiries
bmb-consult – PR-Agentur der GMH Gruppe
Simone Boehringer
Senior Editor & Senior Account Manager
GMH Gruppe
Luciana Filizzola
Director Sustainability and Communications