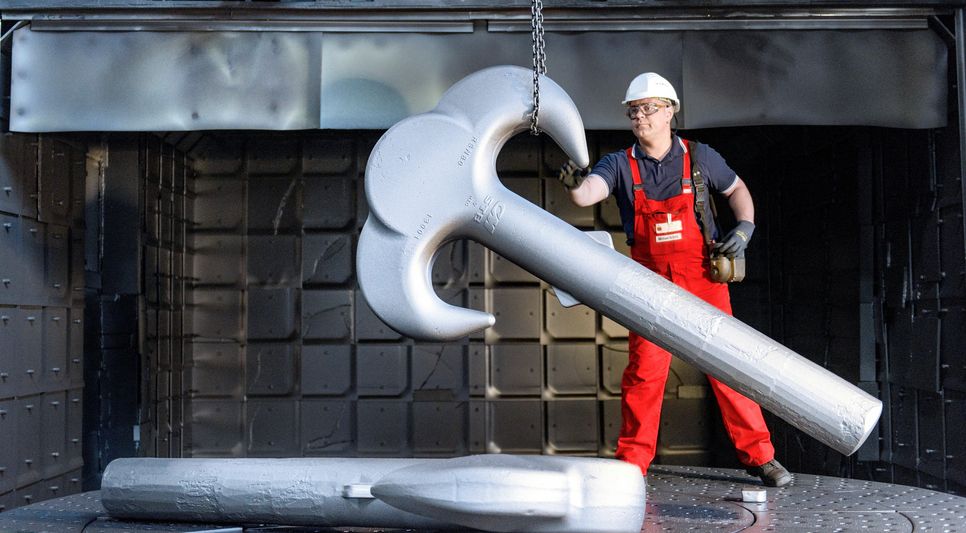
Wildau, August 18, 2023
Investment in the future: WSK forges ahead with lower emissions and higher efficiency
Wildauer Schmiede- und Kurbelwellentechnik GmbH (WSK) is investing a total of around 2.5 million euros in two new heating furnaces and a modern charging system. As part of a transformation program towards climate neutrality lasting many years, the company is not only reducing the CO2 footprint of its products through energy savings, but also increasing productivity as a result.
WSK, which is part of GMH Group, is shaping its future with a modern thermoprocessing plant. By investing in three key components of this system – heating furnaces, charging unit and the forging hammer line – the company from Wildau, Brandenburg, aims to perfect interaction of these elements and thus to significantly increase productivity and quality. WSK is already today one of the few companies in Europe that has a 630 Kilojoule forging hammer and can use it to produce large components for mechanical and plant engineering, for railroad technology, and in the future, also for new applications such as industrial heat pumps.
The installation of the new plant is part of a major transformation process at WSK, with which the Wildau-based company aims to sustainably improve its market position in ecological terms. One example of this is the target of reducing CO2 emissions by 50 percent compared with the 2019 level to around 0.65 tons per ton of steel supplied by 2030. Savings of more than 7 percent have already been achieved in recent years.
The biggest lever here is the reduction of around one-third of total energy requirements – mainly gas and electricity, but also district heating – by 2030. WSK aims to achieve this ambitious target with a whole range of measures, some of whose effects will only be fully felt in the coming years. These range from switching to energy-saving LED lights and, in the long term, a share of up to 35 percent green electricity, to a more efficient supply of compressed air as well as the use of waste heat for heating and the use of hydrogen instead of natural gas in the heating furnaces.
“This package of measures is designed to put WSK on course for growth and make it future-proof: With a product portfolio that only a few companies in Europe can deliver, with energy-saving and efficient processes, and with a clear commitment to securing existing jobs and, in perspective, creating new ones in the region,” says Dr. David Biere, Commercial Director and Deputy Plant Director of Wildauer Schmiede- und Kurbelwellentechnik GmbH.
„Dieses Maßnahmenpaket soll WSK auf Wachstumskurs bringen und zukunftssicher machen: Mit einem Produktportfolio, das in Europa nur wenige Unternehmen liefern können, mit energiesparenden und effizienten Prozessen und mit einem klaren Bekenntnis zur Sicherung bestehender und perspektivisch auch zur Schaffung neuer Arbeitsplätze in der Region“, sagt Dr. David Biere, Kaufmännischer Leiter und stellvertretender Werksleiter der Wildauer Schmiede- und Kurbelwellentechnik GmbH.
Natural gas savings equivalent to the annual consumption of 150 average households
Previously, the production process at WSK would involve the steel ingots being heated in three old furnaces before they were individually extracted out of the furnace red-hot by the gripper and placed under one of the forging hammers for forging. In the future, this heating process will be carried out by the two new, significantly more efficient, furnaces. Additionally, these can be operated using hydrogen, which can be used to replace natural gas in the long term when firing the furnaces. In the medium term, it is already possible to use hydrogen as an admixture in the heating process.
In addition, two steps in the preparation of the forging process can now take place in parallel: the rough forging and the planning of the forging. This reduces waiting times before inserting the steel under the hammer – and also eliminates the need to reheat the steel for the actual forging process. Based on the current annual production mix, WSK will be able to save around 7 percent of their natural gas consumption per year compared to 2019. This is roughly equivalent to the annual gas consumption of around 150 average-sized apartments in Germany. Thanks to the good interaction of the individual plant components and the resulting improvement in energy efficiency, the CO2 footprint of the products from Wildau will be significantly reduced once again.
Compared to the existing charging system, the new unit offers significantly improved functional options. For example, the ingot to be forged can not only be gripped and placed in or extracted, it can also be rotated and placed under a forging hammer as required. This allows for faster and more precise access to the two furnaces, which in turn supplies the H63 forging hammer with more material and enables it to process higher volumes.
The two new furnaces are scheduled to start operation as early as the beginning of next year, with the new charging system going into regular operation in the summer of 2024.
Wildauer Schmiede- und Kurbelwellentechnik GmbH
Wildauer Schmiede- und Kurbelwellentechnik GmbH, based in Wildau, Brandenburg, manufactures large closed-die forgings and ready-to-install crankshafts. The company is part of GMH Gruppe and supplies safety-critical and other components made of low- to high-alloy steels, most of which are sourced from within the group, resulting in a low carbon footprint. The broad product portfolio includes connecting rods and crankshafts for large engines and components for use in rolling stock, mechanical and plant engineering, the food industry and other sectors. The high product quality standard required for decades of use has been confirmed by renowned customers worldwide for many years.
About GMH Gruppe
GMH Gruppe is a full-range supplier of recycled input material through ready-to-install components and one of the largest privately owned metalworking companies in Europe. The Gruppe comprises 15 medium-sized production companies in the steel, forging and casting industry and is present in more than 50 countries. With around 6,000 employees, the GMH Gruppe generated annual sales of around two billion euros in 2021.
GMH Gruppe is a pioneer in sustainable steel production and has also been accepted into the “Association of Climate Protection Companies”. By recycling scrap metal, the company produces green steel and thus makes an important contribution to the circular economy. The use of electric arc furnaces at four of its sites reduces carbon dioxide emissions by a factor of five compared with conventional blast furnaces. This, in turn, also reduces the carbon footprint of GMH’s customers.
Global customers include companies from the automotive industry, mechanical and plant engineering, railroad technology, power generation, transport logistics as well as the sectors, aerospace, agriculture and construction machinery.
The GMH Gruppe has set itself the goal of being completely climate-neutral by 2039.
For inquiries
GMH Gruppe
Martina Wülfrath
Communications Wildauer Schmiede- und Kurbelwellentechnik GmbH