Steel castings
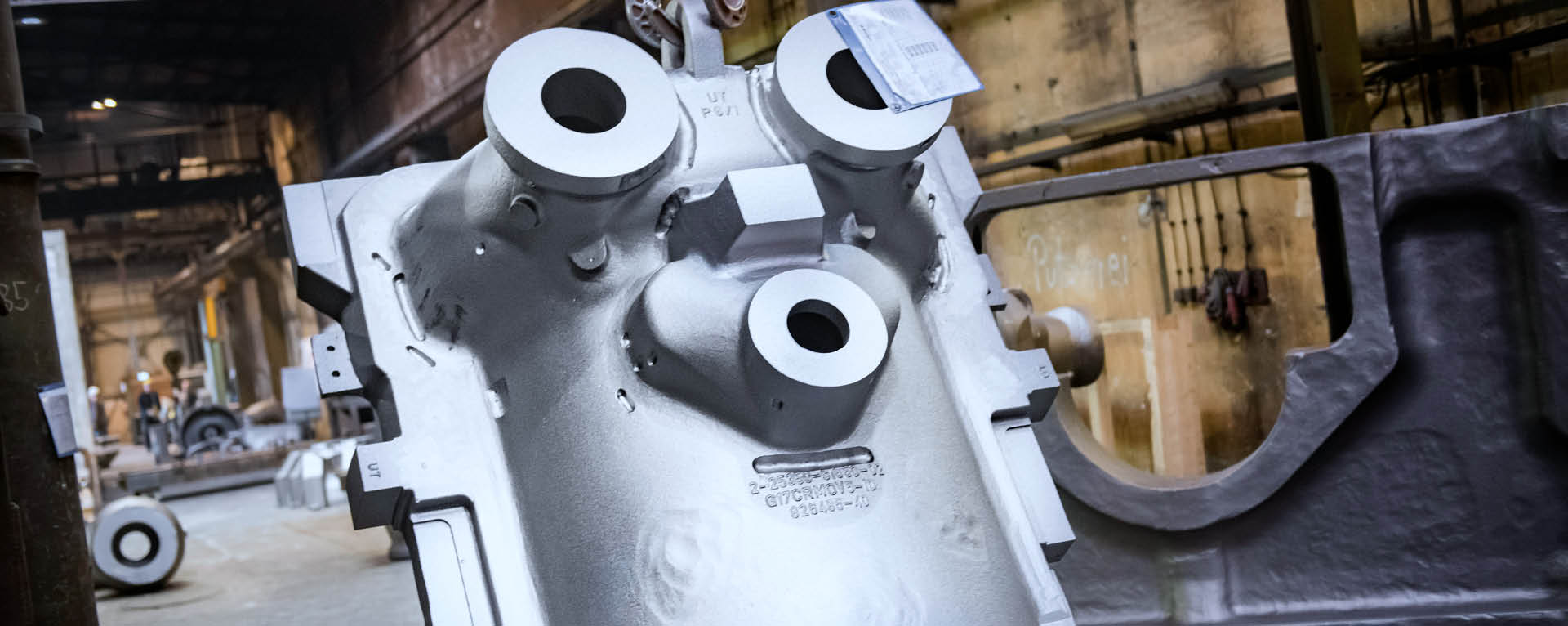
We produce high-quality cast steel components for well-known customers in the oil and gas, energy, railroad, mechanical engineering and defense technology industries, among others. We offer prototypes as well as small and medium-sized series.
Steel is produced in electric arc and induction crucible furnaces with subsequent VOD treatment. In the further process, we have various further processing options such as fettling, production welding, construction welding, heat treatment and surface treatment as well as comprehensive quality control including X-ray inspection. We also have our own mechanical processing facilities.
specifications
Our Portfolio
Stahlguss
We cover a wide range of unalloyed and low-alloy steels, high-alloy steels and stainless steels including duplex and super-duplex steel castings as well as 6-mo
austenites, Ni-base alloys and hardfacing steel castings. In addition, we manufacture all common types of high-alloy, austenitic cast iron with spheroidal carbon formation (NiResist).
Application:
High-pressure fittings in the oil and gas industry, chassis components in streetcars, compressor components for large plants, (turbine) housings and valve combinations for the energy sector, machine components for the rubber industry, ingot casting (starting material for forging)
Contact
We manufacture all our products to customer specifications. So what are your specifications?
Please feel free to contact us. Together we will find your perfectly customized solution.
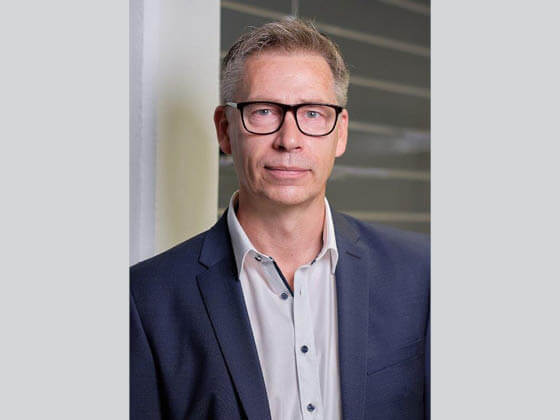
Oliver Hölscher
Sales Director Castings Pleissner Guss GmbH
Further processing possibilities
Heat treatment
Quenched and tempered (water or air hardening)
(+QT)
Normalising annealed
(+N)
Solution annealed
(+AT)
Stress-relieved annealed
(+S)
Quenching media
air, air blast, polymer, water
Mechanical processing options
Turning
max. Ø 2.300 mm * 2.100 mm
Milling
max. x: 2.200 mm, y: 1.600 mm, z: 1.850 mm
drilling
sawing
Surface treatment
Coloring
(external)
Staining
(external/internal)
GS/GX blasting
(internal)
corundum blasting
(external)
What you can expect
100% raw material recycling
We use almost 100% scrap in steel production, thereby enabling closed material cycles
Simulation processes
The simulation of the casting and solidification process using state-of-the-art software enables us to influence the casting-compatible design of future cast parts in the design and planning phase
Linear accelerators
We use a linear accelerator that enables us to blast components with wall thicknesses of up to approx. 300 mm