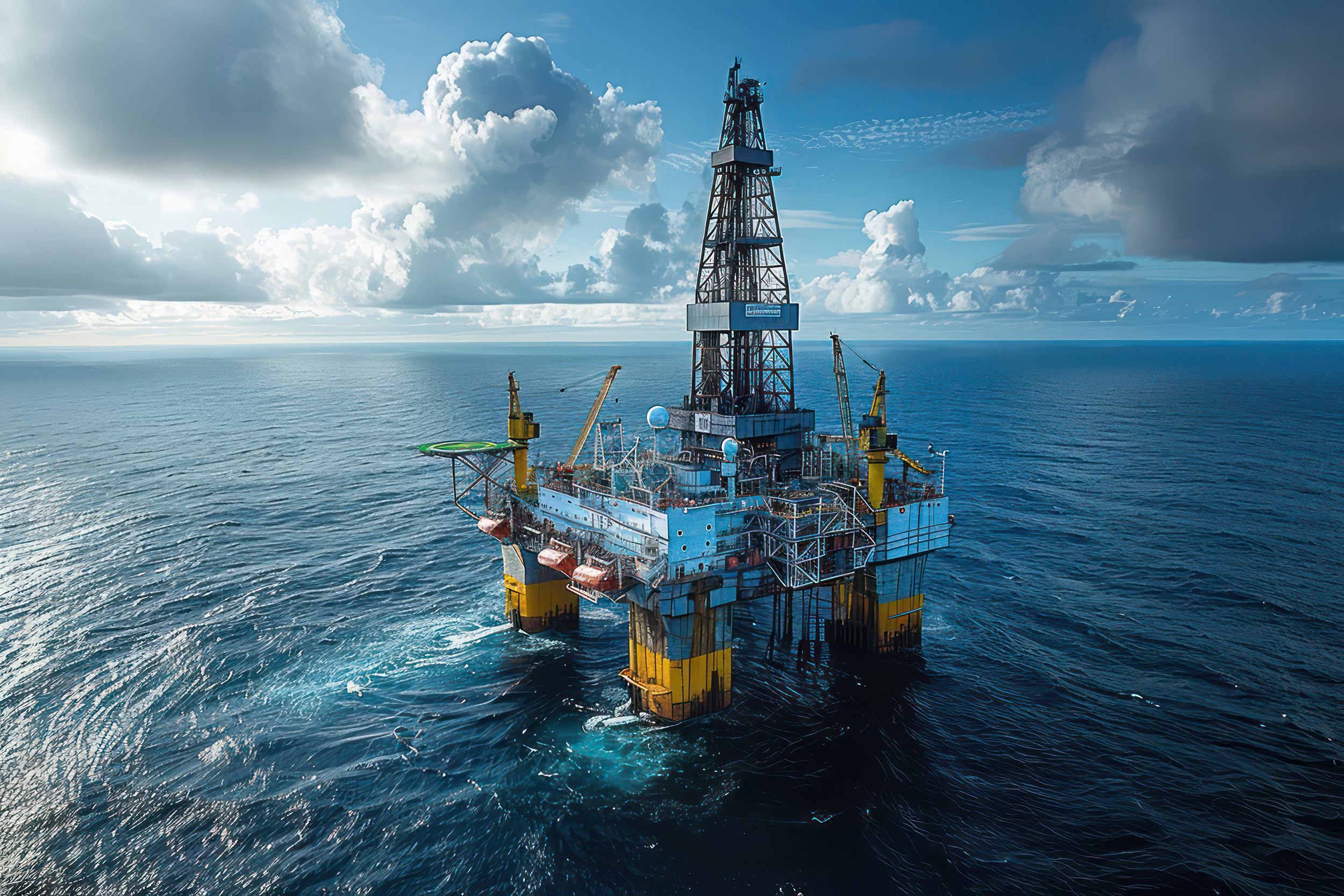
Cronidur® 30 als Gamechanger im Offshore-Bereich
Kaum etwas auf unserem Planeten ist stärker als die Naturgewalten. Sie verlangen Konstruktionen und Werkstoffen alles ab – speziell in den Tiefen des Meeres. Diesen Kräften sah sich auch eine unbemannte Offshore-Plattform vor Norwegen ausgesetzt. Der Einsatz im Subsea-Bereich erforderte die Entwicklung eines robusten Motor-Kompressor-Designs, das den extremen Bedingungen unter Wasser standhalten konnte.
Herausforderung: Korrosionsbeständigkeit unter extremen Bedingungen
„Dem Kunden sind die Bauteile weggerostet“, erinnert sich das Team der GMH Gruppe, an den Anfang der Zusammenarbeit. Ein Ersatz für den bisherigen Werkstoff 1.3505 (100Cr6) musste her, der den hohen Korrosionsanforderungen des Einsatzes in Seewasser standhält. Ein zentrales Problem, dem die bisherigen Materialien für Lager in den Kompressoren nicht ausreichend widerstehen konnten.
Cronidur® 30: Der Schlüssel zum Erfolg
Den GMH-Experten war schnell klar, dass für dieses Projekt nur Cronidur® 30 als idealer Ersatz in Frage kam. Die ausgezeichnete Qualität dieses Werkstoffs, der nach strengen ISO-Normen zusätzlich erprobt und qualifiziert ist, bot entscheidende Vorteile:
- außergewöhnliche Korrosionsbeständigkeit,
- überragende Langlebigkeit sowie Zähigkeit
- herausragende Härte, ideal für extreme Bedingungen
Diese Eigenschaften machten Cronidur® 30 zur optimalen Lösung für den Einsatz unter Wasser.
Prototypen und Fertigungsprozesse
Doch die Auswahl des richtigen Werkstoffs war nur der erste Schritt. Es folgten Prototypen der Fanglagerbüchsen und Wellenmuttern, die die Ingenieure der GMH Gruppe mit hoher Präzision entwickelten. Vor dem Einsatz durchliefen die Bauteile strenge Prüfungen, darunter eine spezielle Wärmebehandlung, die das Team in Zusammenarbeit mit dem Kunden erarbeitet hatte. Diese Behandlung gewährleistete, dass die mechanischen Eigenschaften – wie Zähigkeit und Härte – den extremen Anforderungen des Unterwassereinsatzes trotzen. Eine abschließende Qualitätsprüfung erfolgte direkt bei der Energietechnik Essen GmbH (ETE), um zu garantieren, dass höchste Standards eingehalten werden.
Für die finale Bearbeitung der Komponenten lieferte die ETE Stab- und Blankstahl in den Abmessungen von 200-250 mm an qualifizierte Bauteilehersteller.
Längere Wartungsintervalle und sinkende Kosten
Dank der verschleißfesten Eigenschaften von Cronidur® 30 kann der Kunde zukünftig Wartungsintervalle verlängern und kostspielige Überholungen von Anlagen in Tiefen von mehr als 1000 m vermeiden. Ein essenzieller Aspekt, der nicht nur wirtschaftliche Vorteile bietet, sondern auch umweltschonend ist.
Nach dem positiven Feedback des Kunden wird das Projekt in enger Zusammenarbeit mit qualifizierten Unternehmen weitergeführt, um den Einsatz von Cronidur® 30 auszubauen. Mit diesem Projekt hat die GMH Gruppe den ersten großen Kontakt in den Subsea-Bereich geknüpft und beweist damit einmal mehr die herausragende Qualität und Innovationskraft ihrer Werkstoffe und Dienstleistungen.
Wollen Sie mit uns
Vorreiter der Dekarbonisierung werden?
Mit uns führen Sie Ihr Unternehmen in eine grüne Zukunft.